Steel vs. Aluminum: The Real Strength Battle for Your Solar Installation
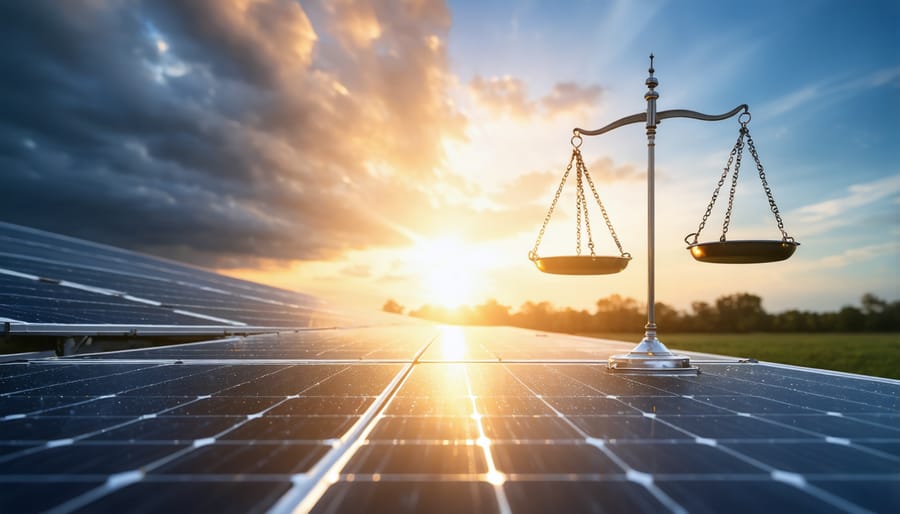
When selecting solar mounting materials, understanding the yield strength difference between steel and aluminum becomes crucial for structural integrity and long-term performance. Steel typically offers yield strength between 250-1000 MPa, while aluminum alloys range from 100-455 MPa, making steel the superior choice for high-stress applications. However, this mechanical advantage comes with important trade-offs in weight and corrosion resistance.
For European installations, where varied climate conditions demand careful material selection, the yield strength-to-weight ratio becomes particularly significant. Aluminum’s lower density (one-third of steel) often compensates for its reduced yield strength, especially in regions where wind and snow loads are moderate. This balance between strength and weight efficiency has made aluminum increasingly popular in modern solar installations, despite steel’s higher absolute yield strength.
The choice between these materials ultimately depends on specific project requirements, installation environment, and load calculations that consider both immediate and long-term structural demands.
Understanding Yield Strength: The Basics
Yield strength represents a critical material property that determines how well a metal can withstand mechanical stress before permanent deformation occurs. Think of it as the threshold where a material stops returning to its original shape when force is applied. For solar mounting systems, this property is particularly crucial as these structures must maintain their integrity while supporting heavy panels and withstanding various environmental forces.
When designing solar installations, understanding yield strength helps ensure long-term reliability and safety. It represents the point at which a material transitions from elastic to plastic deformation – essentially, the moment when temporary bending becomes permanent damage. This characteristic is measured in megapascals (MPa) or pounds per square inch (psi), providing engineers and installers with clear parameters for safe design limits.
In solar mounting applications, yield strength directly influences several key factors:
– The maximum weight of solar panels a structure can support
– Resistance to wind loads and environmental stresses
– Long-term structural integrity of the installation
– Safety margins in extreme weather conditions
For European installations, where weather conditions can vary significantly between regions, yield strength becomes even more relevant. From the snow loads in Alpine regions to strong coastal winds, mounting systems must maintain their structural integrity across diverse environmental challenges. This makes yield strength a fundamental consideration when choosing between steel and aluminum for solar mounting solutions.

Steel’s Yield Strength Profile
Common Steel Grades in Solar Applications
In solar installations across Europe, several steel grades have proven their reliability and effectiveness for solar panel mounting frames and support structures. The most commonly used grade is S235, which offers an excellent balance of strength, workability, and cost-effectiveness. This versatile steel grade provides a yield strength of approximately 235 MPa, making it suitable for most residential and commercial solar installations.
For more demanding applications, S355 steel has become increasingly popular, particularly in regions with heavy snow loads or strong winds. With a yield strength of 355 MPa, this grade delivers enhanced structural integrity while maintaining reasonable fabrication characteristics.
Hot-dip galvanized versions of these grades (S235Z and S355Z) are frequently specified to ensure long-term corrosion resistance, crucial for outdoor solar installations. The zinc coating provides an additional protective layer that can extend the service life of the installation by several decades.
For specialized applications, such as coastal installations or areas with aggressive environmental conditions, stainless steel grades like 1.4301 (304) and 1.4401 (316) offer superior corrosion resistance. While these options come at a higher initial cost, their durability and minimal maintenance requirements often justify the investment in challenging environments.
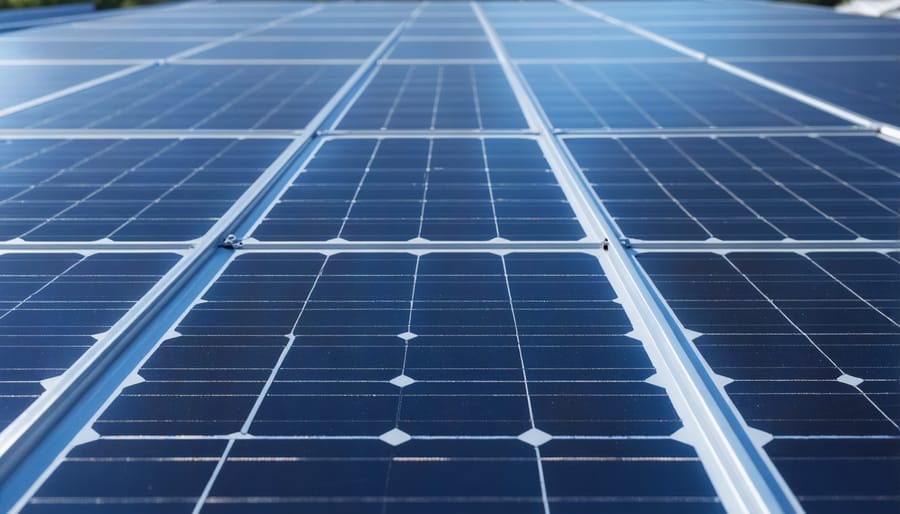
Steel’s Performance Under Stress
Steel exhibits remarkable performance characteristics under various stress conditions, making it a preferred material for structural applications in solar installations. When subjected to loads, steel demonstrates a predictable and linear elastic behavior up to its yield point, allowing engineers to design with confidence. This consistency in performance is particularly valuable for regions experiencing significant snow loads or high wind conditions.
The material’s high yield strength means it can withstand substantial stress before experiencing permanent deformation. In typical solar mounting applications, steel maintains its structural integrity even under combined forces from equipment weight, environmental factors, and dynamic loads. This resilience is especially important for large-scale commercial installations where structural reliability is paramount.
Steel’s ductile nature provides an additional safety advantage. Rather than sudden failure, steel structures typically show visible signs of stress through gradual deformation, allowing for preventive maintenance. This characteristic is particularly beneficial in areas prone to severe weather events or seismic activity.
Temperature variations, common in outdoor solar installations, have minimal impact on steel’s performance within normal operating ranges. The material maintains consistent strength properties across the temperature fluctuations typically encountered in European climate conditions, ensuring year-round structural stability and safety for solar array installations.
Aluminum’s Yield Strength Characteristics
Aluminum Alloys in Solar Mounting
In the solar mounting industry, several aluminum alloys have proven particularly effective, with 6000-series alloys leading the way. The 6061-T6 and 6005A-T6 alloys are widely favoured across European solar installations for their excellent balance of strength and corrosion resistance. These alloys typically offer yield strengths ranging from 170 to 250 MPa, making them robust enough for most mounting applications while remaining significantly lighter than steel alternatives.
The 6082-T6 alloy, particularly popular in Northern European markets, demonstrates superior strength characteristics with yield strengths up to 260 MPa. This alloy performs exceptionally well in coastal environments, where corrosion resistance is paramount. For more demanding applications, such as large-scale commercial installations, the 7000-series alloys offer even higher yield strengths, though they’re less commonly used due to cost considerations.
The choice of aluminum grade significantly impacts system longevity and installation efficiency. Modern mounting systems typically employ these alloys in various components:
– Rail systems (often 6061-T6)
– Clamps and brackets (commonly 6005A-T6)
– Support structures (frequently 6082-T6)
– Connection elements (various grades based on load requirements)
When selecting aluminum alloys for solar mounting, considerations extend beyond mere strength to include factors such as thermal expansion, weather resistance, and compatibility with other system components. The material’s natural corrosion resistance and lightweight properties continue to make it an increasingly popular choice in sustainable energy installations across Europe.
Aluminum’s Load-Bearing Capabilities
Aluminum’s load-bearing capabilities are particularly noteworthy in solar installations, offering a robust balance between strength and weight efficiency. When properly engineered, aluminum structures can support significant loads while maintaining their structural integrity. Typical aluminum alloys used in solar mounting systems demonstrate yield strength ranging from 150 to 300 MPa, depending on the specific grade and treatment.
In practical applications, aluminum demonstrates excellent performance under distributed loads, making it ideal for solar panel support structures. Its strength-to-weight ratio is particularly advantageous, allowing for easier handling during installation while maintaining necessary structural support. When exposed to environmental stresses, aluminum forms a protective oxide layer that prevents further corrosion, ensuring long-term stability.
However, it’s essential to consider that aluminum’s load-bearing capacity can vary significantly with temperature changes. The material typically maintains its structural integrity well between -20°C and 80°C, a range that encompasses most European climate conditions. For solar installations, this translates to reliable performance throughout seasonal variations.
The material’s flexibility also plays a crucial role in its load-bearing capabilities. While this might require additional reinforcement in some cases, it often serves as an advantage by allowing the structure to better absorb and distribute dynamic loads from wind and snow, common concerns in European installations.
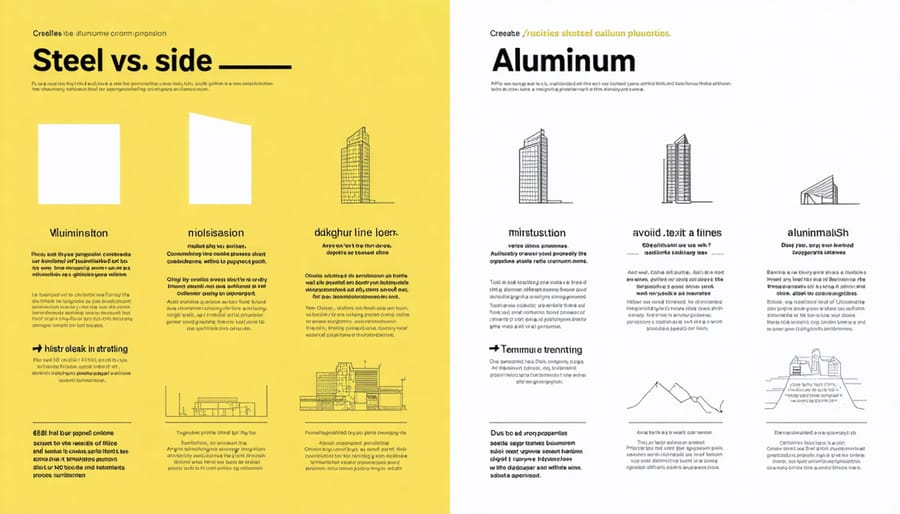
Direct Comparison: Steel vs. Aluminum
When comparing steel and aluminum directly, the yield strength differences become immediately apparent. Structural steel typically offers yield strengths ranging from 250 to 500 MPa (megapascals), while aluminum alloys commonly used in solar panel installation projects generally provide yield strengths between 100 to 300 MPa.
This substantial difference means steel can withstand significantly higher loads before permanent deformation occurs. For instance, a steel beam rated at 350 MPa can support approximately twice the load of a similarly sized aluminum beam rated at 175 MPa before yielding. However, this strength advantage comes with added weight – steel is roughly three times heavier than aluminum.
The practical implications of these differences are crucial for structural applications. While steel’s higher yield strength makes it ideal for heavy-duty support structures and areas with extreme weather conditions, aluminum’s lighter weight combined with adequate strength makes it particularly suitable for rooftop installations where weight distribution is a critical factor.
For most residential and commercial applications, aluminum’s yield strength proves sufficient while offering additional benefits such as corrosion resistance and easier handling during installation. Steel remains the preferred choice for ground-mounted systems and areas requiring exceptional structural integrity.
In comparing steel and aluminum for structural applications, particularly in solar installations, both materials present distinct advantages that suit different project requirements. Steel’s superior yield strength, typically ranging from 250-1000 MPa, makes it the preferred choice for heavy-duty applications where maximum load-bearing capacity is essential. Aluminum, while offering lower yield strength of 70-700 MPa, compensates with its excellent strength-to-weight ratio and superior corrosion resistance.
For European solar installations, the choice between these materials should consider local climate conditions, installation requirements, and long-term maintenance needs. In coastal regions, aluminum’s natural corrosion resistance offers significant advantages, while inland areas might benefit from steel’s cost-effectiveness and higher strength. Project planners should carefully evaluate factors including budget constraints, structural loads, and environmental exposure.
The optimal material selection ultimately depends on specific project parameters. We recommend consulting with structural engineers for detailed analysis, particularly for large-scale installations where material choice significantly impacts project success and long-term sustainability.
Leave a Reply