Solar Heat Powers Industry: Transforming European Manufacturing With Thermal Solutions
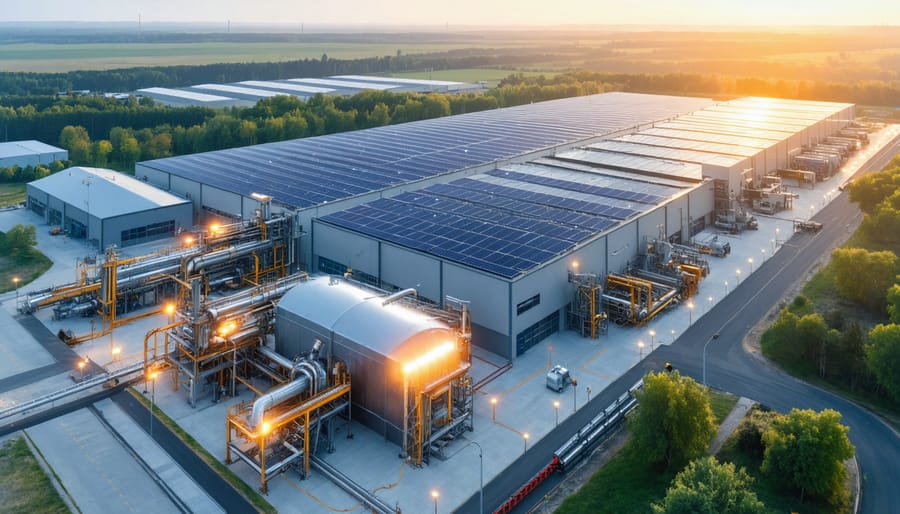
Transform your industrial energy landscape with advanced thermal solutions that merge cutting-edge technology with sustainable practices. Today’s manufacturing facilities face unprecedented pressure to reduce carbon emissions while maintaining operational efficiency – making solar thermal manufacturing solutions increasingly critical for forward-thinking businesses.
Modern industrial thermal systems offer a triple advantage: significant cost reduction through energy efficiency, enhanced process control through precise temperature management, and substantial environmental benefits through reduced carbon emissions. From food processing to chemical manufacturing, these innovative solutions are revolutionizing how European industries approach their heating and cooling needs.
With energy costs continuing to rise across Europe, industrial thermal solutions represent not just an environmental choice, but a strategic business decision. Advanced heat recovery systems, smart temperature control networks, and hybrid solar-conventional installations are delivering payback periods as short as 2-3 years while reducing operational costs by up to 60%.
Whether upgrading existing facilities or planning new installations, today’s thermal solutions offer unprecedented flexibility and efficiency. The integration of IoT sensors, predictive maintenance systems, and automated control mechanisms ensures optimal performance while minimizing downtime and maximizing return on investment.
The Power of Industrial Solar Thermal Systems
Process Heat Generation
Solar thermal systems harness the sun’s energy through advanced collector technologies to generate process heat for various industrial applications. These systems typically employ evacuated tube collectors or concentrated solar power (CSP) arrays that capture solar radiation and convert it into usable thermal energy.
The process begins when sunlight strikes the collectors, where a heat transfer fluid – usually water, thermal oil, or glycol – circulates through the system. This fluid absorbs the solar energy and can reach temperatures between 80°C and 400°C, making it suitable for diverse industrial processes such as drying, sterilization, and chemical processing.
The heated fluid then transfers its thermal energy through heat exchangers to the industrial process requiring heat. Modern systems incorporate thermal storage solutions, allowing industries to maintain consistent heat supply even during cloudy periods or nighttime operations.
Integration with existing industrial heating systems is streamlined through sophisticated control systems that ensure optimal heat distribution and system efficiency. This sustainable approach to process heat generation significantly reduces fossil fuel dependency while maintaining reliable industrial operations, contributing to both environmental goals and operational cost reduction.
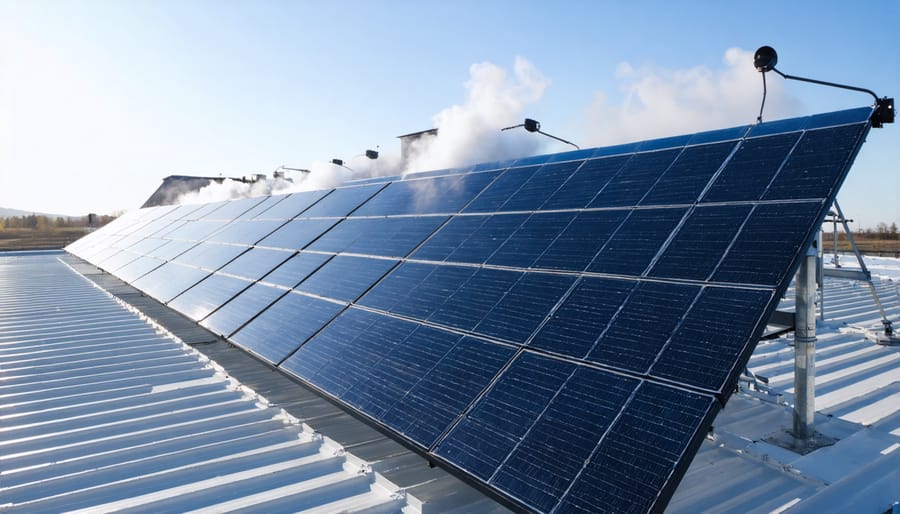
Temperature Ranges and Capabilities
Modern industrial thermal solutions offer remarkable temperature flexibility, ranging from low-temperature applications at 60°C to high-intensity processes reaching 400°C. This broad spectrum enables diverse industrial applications, from food processing and textile manufacturing to chemical production and metalworking.
For low-temperature processes (60-120°C), solar thermal systems excel in applications like pasteurisation, washing, and drying operations. Medium-temperature ranges (120-250°C) support industrial processes such as sterilisation, steam generation, and distillation, making them particularly valuable in pharmaceutical and food industries.
High-temperature capabilities (250-400°C) enable more energy-intensive processes, including chemical reactions and certain metallurgical operations. Advanced solar thermal collectors, especially concentrated solar systems, can efficiently deliver these temperatures while maintaining operational stability.
The integration of thermal storage solutions extends these capabilities beyond daylight hours, ensuring consistent temperature maintenance for continuous industrial processes. This flexibility, combined with precision temperature control, makes modern thermal solutions increasingly attractive for industries seeking sustainable process heat alternatives.
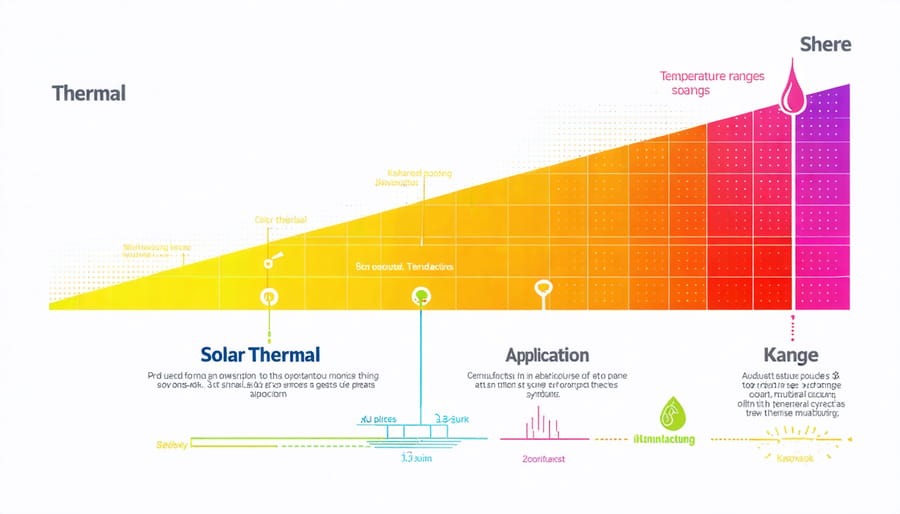
Key Industrial Applications
Manufacturing and Processing
Industrial thermal solutions play a pivotal role in transforming European manufacturing processes, particularly in critical operations such as drying, sterilization, and cleaning. These applications leverage solar thermal technology to deliver consistent, reliable heat for various industrial requirements while reducing operational costs and environmental impact.
In drying applications, solar thermal systems provide the precise temperature control needed for products ranging from textiles and paper to food products and agricultural materials. The technology ensures uniform heat distribution, maintaining product quality while significantly reducing energy consumption compared to conventional heating methods.
Sterilization processes in pharmaceutical, food, and beverage industries benefit from industrial thermal solutions through the delivery of high-temperature steam and hot water. These systems maintain strict hygiene standards while offering substantial energy savings and operational efficiency. The integration of smart controls ensures temperature consistency and process reliability, crucial for maintaining product safety and regulatory compliance.
Industrial cleaning operations utilize thermal solutions for applications such as tank cleaning, equipment sanitization, and process vessel maintenance. The ability to deliver hot water at specific temperatures makes these systems particularly valuable in industries where cleanliness is paramount, such as dairy processing and chemical manufacturing.
Modern thermal solutions incorporate advanced heat recovery systems and thermal storage capabilities, enabling continuous operation even during periods of limited solar radiation. This innovation ensures manufacturing processes remain uninterrupted while maximizing the benefits of renewable energy integration.
Metal Treatment and Mining
In metal processing and mining operations, thermal solutions play a crucial role in optimizing efficiency and reducing environmental impact. Advanced solar thermal technologies are revolutionizing traditional metal treatment processes, offering sustainable alternatives for heating, melting, and refining operations. These systems are particularly effective in pre-heating processes, reducing the energy required for subsequent high-temperature treatments.
The integration of thermal solutions in metal processing includes applications such as annealing, tempering, and surface treatment, where precise temperature control is essential for product quality. Modern installations utilize hybrid systems that combine solar thermal collectors with conventional heating methods, ensuring consistent performance while significantly reducing carbon emissions.
Solar applications in mining have demonstrated remarkable success in mineral processing and extraction operations. These installations help power thermal desorption processes, heap leaching, and electrowinning operations, delivering substantial energy savings while maintaining operational reliability.
The implementation of smart monitoring systems ensures optimal temperature management throughout these processes, while heat recovery systems maximize energy efficiency by capturing and recycling waste heat. This integrated approach not only improves operational efficiency but also helps industries meet increasingly stringent environmental regulations while reducing operational costs.
Implementation and Integration
System Design Considerations
Designing an effective industrial solar thermal system requires careful consideration of multiple interconnected factors. The system’s performance and efficiency heavily depend on the facility’s geographical location, available roof or ground space, and local climate conditions. These elements directly influence the solar collector type selection and system dimensioning.
Load profile analysis is crucial, as industrial processes often have specific temperature requirements and usage patterns. Engineers must evaluate both the peak demand and daily consumption patterns to ensure optimal system sizing. This includes accounting for seasonal variations and potential production schedule changes.
Integration with existing heating systems demands particular attention. The solar thermal solution should complement conventional heating methods seamlessly, often through sophisticated control systems that optimize energy distribution. Heat storage capabilities are equally important, allowing excess thermal energy to be stored during peak production periods for later use.
System modularity and scalability should be considered during the initial design phase, enabling future expansion as needs grow. Material selection must account for process-specific requirements, such as temperature resistance and compatibility with industrial fluids.
Safety considerations and regulatory compliance play vital roles, particularly in high-temperature applications. This includes pressure management, overflow protection, and emergency shutdown systems. Regular maintenance access points should be incorporated into the design, ensuring long-term system reliability and performance optimization.
The financial viability of the system depends on careful balance between initial investment, operational costs, and expected energy savings. Modern designs increasingly incorporate smart monitoring systems for real-time performance tracking and predictive maintenance.
Integration with Existing Infrastructure
Successful industrial solar integration requires a methodical approach to merge new thermal solutions with existing infrastructure. The key lies in conducting thorough system audits and identifying integration points that minimize disruption while maximizing efficiency gains.
Modern solar thermal systems are designed with adaptability in mind, featuring standardized connections and modular components that facilitate seamless incorporation into current heating networks. This flexibility allows facilities to maintain their conventional heating systems as backup while gradually transitioning to solar thermal power.
The integration process typically begins with an assessment of current heat demands, temperature requirements, and available space. Engineers then design custom interface solutions, such as heat exchangers and control systems, that enable smooth interaction between solar thermal collectors and existing industrial processes.
Smart monitoring systems play a crucial role in managing the hybrid setup, automatically balancing solar thermal input with conventional heating sources based on real-time demand and availability. This intelligent control ensures optimal performance while maintaining process stability.
To minimize downtime during installation, integration work is often scheduled during planned maintenance periods. This approach, combined with careful planning and modular implementation, enables industries to upgrade their thermal systems without compromising production schedules.
Economic and Environmental Benefits
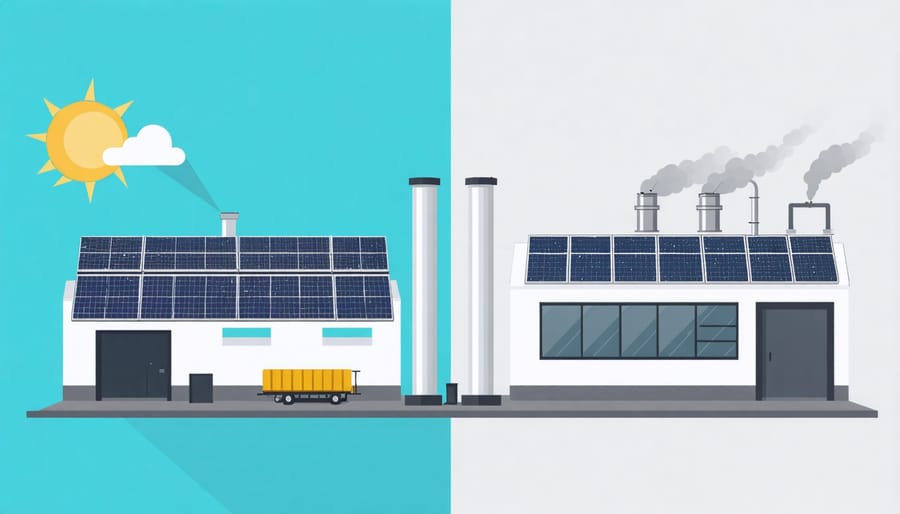
Return on Investment
Investing in industrial thermal solutions delivers substantial financial returns through multiple channels. Most systems achieve payback periods ranging from 3 to 7 years, depending on the installation scale and energy consumption patterns. For large industrial facilities, annual energy cost reductions typically range from 30% to 60%, with some enterprises reporting savings of up to €150,000 per year.
The return on investment is particularly attractive when considering current European energy prices and available government incentives. Many EU member states offer grants, tax benefits, and subsidies that can reduce initial installation costs by 20-40%. This significantly accelerates the payback period and enhances long-term profitability.
Beyond direct energy savings, these systems provide additional financial benefits through reduced maintenance costs, increased equipment longevity, and improved production efficiency. Companies also report enhanced market competitiveness due to lower operational costs and improved sustainability credentials. When factoring in rising energy costs and stricter environmental regulations, the long-term economic advantages become even more compelling for industrial operators considering thermal solution implementation.
Carbon Footprint Reduction
Industrial thermal solutions play a crucial role in reducing carbon emissions across European manufacturing and processing facilities. By integrating solar thermal systems into industrial processes, businesses can significantly decrease their reliance on fossil fuels, leading to substantial CO2 reductions. A typical industrial solar thermal installation can reduce carbon emissions by 40-60% compared to conventional heating methods.
The environmental impact extends beyond direct carbon savings. These systems help industries meet strict EU sustainability targets while contributing to national climate goals. For instance, a medium-sized facility implementing solar thermal solutions can achieve carbon reductions equivalent to planting 5,000 trees annually.
Modern industrial thermal systems also incorporate smart monitoring and optimization features that ensure maximum efficiency and minimal waste. This technological advancement helps businesses maintain optimal performance while continuously reducing their environmental footprint. Additionally, the integration of thermal storage solutions enables facilities to maximize solar energy utilization, further decreasing reliance on carbon-intensive backup systems.
By choosing solar thermal solutions, industries demonstrate environmental leadership while securing long-term sustainability benefits for their operations and local communities.
Future Outlook
The industrial solar thermal sector is poised for significant transformation in the coming years, driven by technological advancements and increasing demand for sustainable energy solutions. Industry experts predict that next-generation thermal storage systems will revolutionize how industries harness and utilize solar energy, enabling 24/7 operations regardless of weather conditions.
Emerging trends include the integration of artificial intelligence and IoT sensors to optimize thermal system performance, leading to improved efficiency and reduced operational costs. These smart systems will automatically adjust to changing weather patterns and production demands, maximizing energy capture and utilization.
In Europe, the development of hybrid systems combining solar thermal with other renewable technologies is gaining momentum. These integrated solutions promise to deliver more reliable and cost-effective energy solutions for industrial processes, particularly in regions with varying seasonal solar conditions.
Materials science breakthroughs are expected to yield more efficient solar collectors and thermal storage media, potentially increasing system efficiency by up to 30% within the next decade. Additionally, modular design approaches are making installation and scaling more accessible for businesses of all sizes.
The European Union’s commitment to carbon neutrality by 2050 is driving increased investment in industrial solar thermal research and development. This includes funding for innovative projects focused on high-temperature applications and advanced thermal storage solutions.
Looking ahead, we can expect to see broader adoption of solar thermal technology in traditionally energy-intensive industries, supported by improved financing options and strengthened policy frameworks. The combination of technological innovation, falling costs, and environmental imperatives positions industrial solar thermal solutions as a cornerstone of sustainable industrial development.
Industrial thermal solutions represent a crucial stepping stone towards a more sustainable and energy-efficient future for European industries. By implementing solar thermal technologies, businesses can significantly reduce their carbon footprint while achieving substantial cost savings in their operations. The integration of these systems, combined with smart monitoring and control solutions, enables unprecedented levels of efficiency in industrial processes.
As we’ve explored throughout this article, the benefits extend far beyond immediate energy savings. From enhanced process reliability to improved regulatory compliance and reduced operational costs, the advantages of industrial thermal solutions are both comprehensive and compelling. The technology’s maturity and proven track record across various industrial applications make it a reliable choice for forward-thinking businesses.
We encourage industrial decision-makers to take the next step in their sustainability journey by conducting a thorough assessment of their thermal energy needs. With available EU incentives and support programmes, there has never been a better time to invest in industrial solar thermal solutions. By embracing these innovations today, industries can position themselves at the forefront of sustainable manufacturing while securing long-term operational efficiency and economic advantages.
Leave a Reply