Solar Cell Testing: How European Labs Ensure Maximum Panel Performance
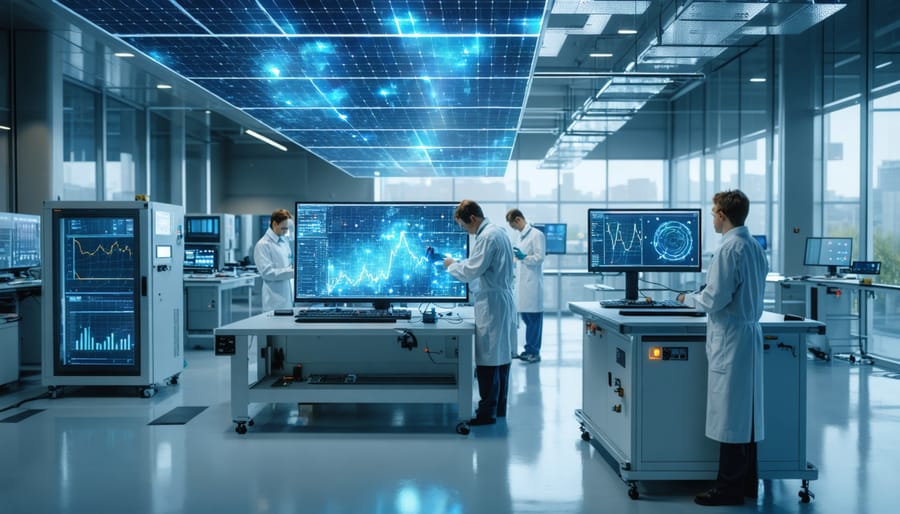
Testing solar cells stands at the intersection of technological innovation and sustainable energy reliability. In modern photovoltaic laboratories across Europe, rigorous testing protocols ensure that solar cells meet strict performance standards before deployment in residential and commercial installations. From precision measurements of conversion efficiency to accelerated stress testing under extreme conditions, these evaluations provide critical data about a cell’s durability, performance, and long-term economic value.
The emergence of standardized testing frameworks, particularly those aligned with IEC and EN certifications, has revolutionized quality assurance in solar technology. Through sophisticated characterization techniques like spectral response analysis and electroluminescence imaging, manufacturers and installers can now predict panel performance with unprecedented accuracy. This scientific approach to validation not only protects investments but also drives continuous improvement in solar cell design and manufacturing processes.
As Europe accelerates its transition to renewable energy, understanding these testing methodologies becomes increasingly vital for stakeholders across the solar value chain. Whether evaluating new installations or monitoring existing arrays, these testing protocols serve as the foundation for reliable, high-performing solar energy systems that meet the continent’s ambitious sustainability goals.
Essential Solar Cell Testing Parameters
Efficiency and Power Output Testing
Testing a solar cell’s efficiency and power output is crucial for meeting solar panel efficiency standards and ensuring optimal performance. The process involves measuring two key parameters: conversion efficiency and maximum power output under standardised test conditions (STC).
Conversion efficiency is determined by exposing the solar cell to a calibrated light source that simulates AM1.5 solar spectrum at 1000W/m² and 25°C. The ratio between the electrical power produced and the incident light power provides the efficiency percentage. Modern testing facilities use high-precision solar simulators and specialized measurement equipment to ensure accuracy within ±2%.
Power output testing evaluates the cell’s current-voltage (I-V) characteristics, identifying the maximum power point (MPP) where the cell operates most efficiently. This involves measuring short-circuit current (Isc), open-circuit voltage (Voc), and fill factor (FF). Advanced testing systems can perform these measurements in milliseconds, providing detailed performance curves.
Temperature coefficients are also measured by testing cells at various temperatures, typically between 15°C and 75°C, to understand performance variations in real-world conditions. This data helps predict actual energy yield in different European climate zones.
Temperature and Environmental Response
Temperature response testing is crucial for understanding how solar cells perform under varying conditions. The process involves measuring power output across different temperatures, typically ranging from -40°C to +85°C, to determine temperature coefficients. These coefficients help predict how a solar cell’s efficiency will change with temperature fluctuations.
Testing chambers simulate real-world conditions by controlling temperature and humidity levels while monitoring cell performance. This provides valuable data about the environmental performance factors that influence solar cell efficiency. Standard test conditions (STC) serve as a baseline, but additional testing at more extreme temperatures ensures reliability in diverse European climates.
Environmental response testing includes exposure to thermal cycling, humidity freeze conditions, and damp heat tests. These procedures evaluate the cell’s resistance to thermal stress, moisture ingress, and potential degradation over time. Modern testing protocols also incorporate UV exposure testing and salt mist resistance, particularly important for installations in coastal regions.
The results from these tests help manufacturers optimize their products for specific climate zones and provide accurate performance warranties, ensuring long-term reliability for European installations.
Advanced Testing Methods and Equipment
Solar Simulators and Light Testing
Solar simulators play a crucial role in testing solar cells under controlled laboratory conditions. These sophisticated devices replicate natural sunlight, allowing manufacturers and researchers to evaluate solar cell performance consistently and reliably. The artificial light sources used typically combine xenon arc lamps or LED arrays to match the solar spectrum as closely as possible.
Modern solar simulators are classified according to three key parameters: spectral match, spatial uniformity, and temporal stability. Class AAA simulators, which meet the highest standards in all three categories, are particularly valued in European testing facilities for their precision and reliability.
The light testing process involves measuring the cell’s response across different wavelengths of light, providing detailed information about its spectral sensitivity. This analysis helps identify how effectively a solar cell converts various parts of the light spectrum into electrical energy. Testing laboratories use specialised spectroradiometers to verify that the simulator’s output matches standardised reference spectra, such as the AM1.5G standard.
Temperature control during light testing is equally important, as solar cell performance varies significantly with temperature. Advanced testing setups include temperature monitoring and regulation systems to ensure consistent test conditions. This attention to detail enables manufacturers to provide accurate performance ratings and helps customers make informed decisions about solar technology investments.
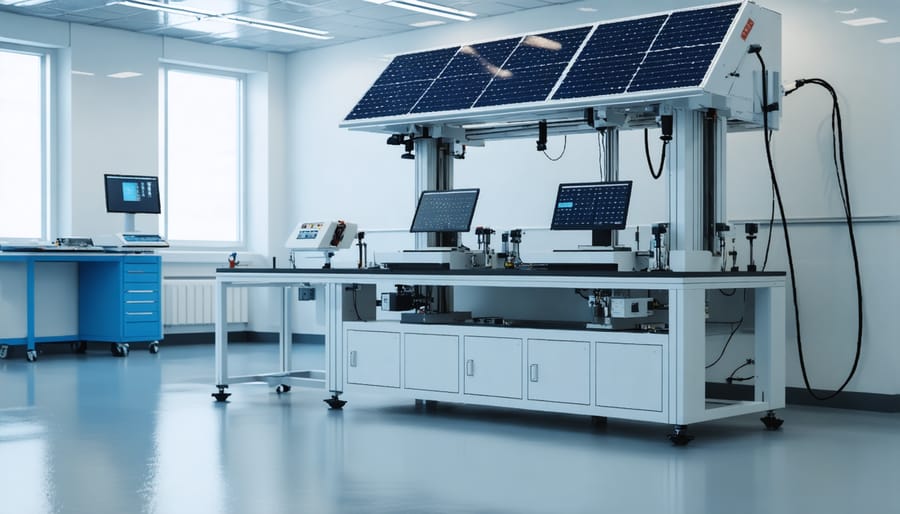
Electrical Performance Analysis
Electrical performance analysis forms the cornerstone of solar cell testing, with the I-V (current-voltage) curve measurement being the primary method for evaluating cell efficiency and power output. During this crucial test, technicians measure the cell’s electrical response across different voltage levels while maintaining consistent illumination conditions.
The I-V curve reveals several vital parameters, including the short-circuit current (Isc), open-circuit voltage (Voc), and maximum power point (MPP). These measurements help determine the cell’s fill factor, which indicates how closely the solar cell performs compared to its theoretical maximum efficiency. Modern testing facilities in Europe utilize precision measurement equipment that can capture these values with accuracy levels of up to ±0.1%.
Performance characterization also includes spectral response testing, which measures how effectively the cell converts light of different wavelengths into electrical energy. This information is particularly valuable for European installations, where varying seasonal light conditions can significantly impact performance.
Quality testing laboratories complement these measurements with temperature coefficient analysis, helping predict how the cell will perform across different operating temperatures. This is especially relevant for regions experiencing extreme temperature variations throughout the year.
The data collected through electrical performance analysis not only validates manufacturer specifications but also provides crucial insights for system designers and installers, ensuring optimal solar installation performance and long-term reliability.
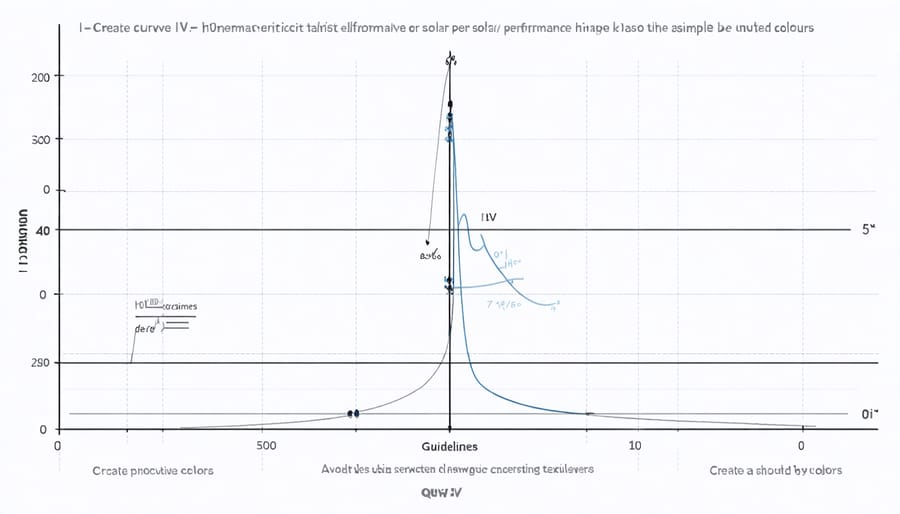
Durability and Stress Testing
Solar cells must withstand various environmental challenges throughout their operational lifetime, making long-term durability testing crucial for ensuring reliable performance. European testing laboratories employ sophisticated methods to simulate decades of weather exposure in accelerated timeframes.
Key stress tests include thermal cycling, where panels undergo rapid temperature fluctuations between -40°C and +85°C to evaluate their resistance to thermal stress. Humidity-freeze testing exposes modules to high moisture levels followed by freezing conditions, simulating harsh winter scenarios common across European regions.
Mechanical load testing applies pressure to simulate snow and wind loads, typically up to 5400 Pascal for snow and 2400 Pascal for wind resistance. Advanced facilities also conduct hail impact tests using ice balls of varying sizes shot at specific velocities to assess impact resistance.
UV exposure testing is particularly important, with specialized chambers subjecting panels to concentrated ultraviolet radiation equivalent to years of sun exposure. This helps evaluate potential degradation of materials and protective coatings.
Modern testing protocols also include salt mist exposure for coastal installations and ammonia resistance testing for agricultural applications. These comprehensive evaluations ensure solar cells meet stringent European quality standards and maintain their efficiency throughout their expected 25-30 year lifespan.
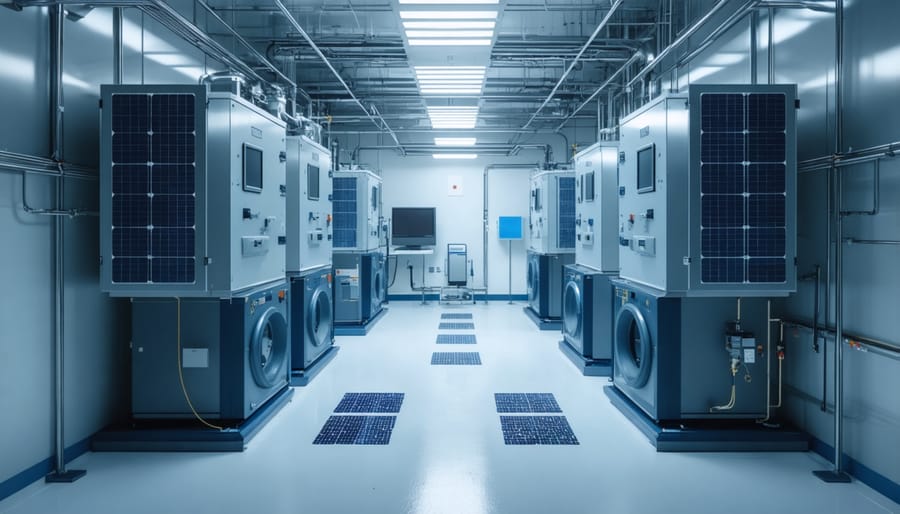
European Certification Standards
IEC Testing Requirements
The International Electrotechnical Commission (IEC) establishes rigorous standards for solar cell testing, ensuring consistent quality and performance across the European market. These requirements form the backbone of solar industry certification, with IEC 61215 and IEC 61730 serving as the primary standards for photovoltaic modules.
IEC 61215 focuses on design qualification and type approval, requiring solar cells to undergo extensive environmental testing. This includes thermal cycling between -40°C and +85°C, humidity-freeze testing, and mechanical load assessments to simulate real-world conditions. Modules must maintain at least 95% of their rated power output after these tests to achieve certification.
For safety considerations, IEC 61730 outlines requirements for construction, testing, and assessment. This standard ensures modules can operate safely throughout their lifetime, addressing electrical safety, fire resistance, and mechanical stability. Testing procedures include hot-spot endurance, bypass diode thermal testing, and insulation resistance measurements.
Additional standards like IEC 62804 address potential-induced degradation (PID), while IEC 61853 evaluates performance under various environmental conditions. Modern testing facilities in Europe must maintain ISO/IEC 17025 accreditation, guaranteeing accurate and reliable results.
For European installations, compliance with these IEC standards is mandatory, providing consumers and businesses with confidence in their solar investments while supporting the continent’s renewable energy objectives.
Quality Assurance Protocols
In Europe, solar cell testing follows strict quality assurance protocols established by the International Electrotechnical Commission (IEC) and European Committee for Standardization (CEN). These protocols ensure that solar cells meet rigorous performance and safety standards before market deployment.
Documentation plays a crucial role in quality assurance, with manufacturers required to maintain detailed records of testing procedures, results, and certification processes. Each solar cell undergoes sequential testing phases, including visual inspection, electrical performance measurement, and environmental stress testing, with results documented at every stage.
The European Solar Test Installation (ESTI) framework provides standardised guidelines for testing facilities across the continent. This harmonised approach enables consistent quality evaluation regardless of testing location, supporting cross-border trade and consumer confidence in solar technologies.
Key documentation requirements include:
– Test sequence reports
– Performance measurement data
– Environmental exposure results
– Safety compliance certificates
– Material composition analysis
– Manufacturing process verification
Quality assurance protocols also mandate regular calibration of testing equipment and validation of measurement procedures. Independent certification bodies conduct periodic audits to verify compliance with these protocols, ensuring transparency and maintaining high industry standards.
For manufacturers and installers, adherence to these protocols isn’t just about regulatory compliance – it’s fundamental to delivering reliable, efficient solar solutions that meet European sustainability goals and consumer expectations.
Future of Solar Cell Testing
The landscape of solar cell testing is rapidly evolving, driven by technological advancements and the growing demands of the renewable energy sector. As emerging solar technologies continue to reshape the industry, testing methodologies are becoming increasingly sophisticated and automated.
Artificial Intelligence and machine learning are revolutionising quality control processes, enabling faster and more accurate defect detection. These smart systems can analyse thermal imaging data, electroluminescence patterns, and performance metrics in real-time, significantly reducing testing time while improving accuracy.
Internet of Things (IoT) integration is another game-changing development, allowing for continuous monitoring and predictive maintenance of solar installations. Advanced sensors can now track performance parameters throughout a panel’s lifetime, providing valuable data for both manufacturers and end-users.
Quantum dot testing technologies are emerging as powerful tools for evaluating next-generation solar cells. These advanced methods can assess the quantum efficiency and spectral response of cells with unprecedented precision, essential for developing higher-efficiency panels.
The European solar industry is particularly focused on developing standardised testing protocols for bifacial solar cells and building-integrated photovoltaics (BIPV). These new standards will ensure consistent quality assessment across diverse installation scenarios.
Looking ahead, we can expect to see more emphasis on environmental impact testing, with new methods being developed to evaluate the full lifecycle sustainability of solar panels. This includes improved recycling potential assessment and carbon footprint analysis during the manufacturing process.
Comprehensive testing of solar cells stands as a cornerstone in advancing renewable energy technology across Europe and beyond. Through rigorous quality assurance processes, we ensure that solar installations deliver optimal performance, longevity, and return on investment for both residential and commercial applications. The systematic evaluation of electrical characteristics, physical durability, and environmental resilience has proven instrumental in driving innovation and improving overall solar cell efficiency.
The impact of thorough testing extends far beyond individual installations. By maintaining high testing standards, the European solar industry continues to lead in quality assurance, fostering trust among consumers and stakeholders while contributing to the continent’s sustainability goals. These testing protocols have enabled manufacturers to refine their production processes, resulting in more reliable and efficient solar solutions.
Looking ahead, the evolution of testing methodologies will remain crucial as solar technology advances. From emerging cell designs to integrated smart systems, comprehensive testing will continue to play a vital role in validating new innovations and ensuring their practical viability. For homeowners and businesses investing in solar energy, this commitment to thorough testing provides the confidence needed to embrace renewable solutions.
As we progress toward a more sustainable future, the significance of solar cell testing cannot be overstated. It serves as the foundation for quality assurance, technological advancement, and the continued growth of Europe’s solar energy sector. Through maintained dedication to testing excellence, we ensure that solar technology remains a reliable, efficient, and future-proof energy solution.
Leave a Reply