PTFE: The Revolutionary Material Making Solar Installations More Efficient
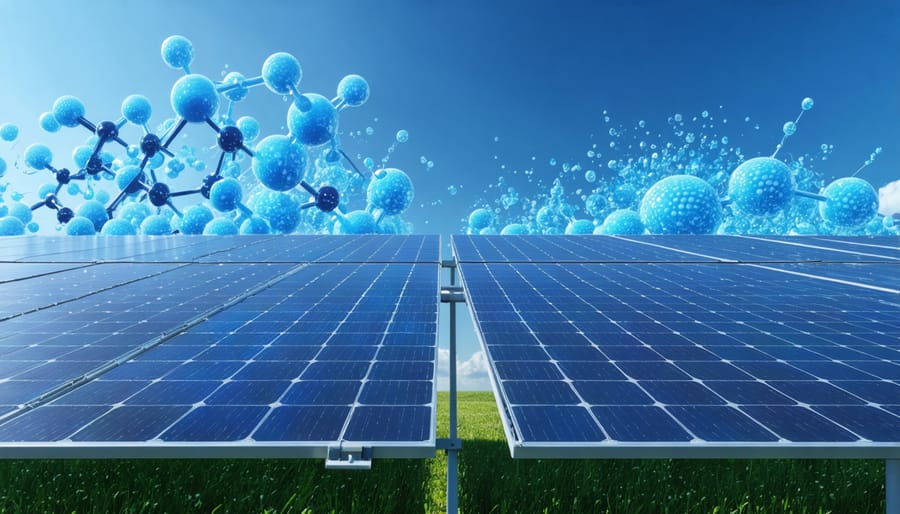
PTFE (Polytetrafluoroethylene) stands as one of modern industry’s most versatile and revolutionary synthetic materials, transforming everything from industrial manufacturing to everyday applications. First discovered in 1938, this remarkable fluoropolymer combines exceptional chemical resistance with outstanding thermal stability, functioning effectively from -200°C to +260°C. Its unique molecular structure, consisting of carbon atoms completely surrounded by fluorine, creates an incredibly stable compound with one of the lowest friction coefficients of any solid material.
In today’s precision-driven industrial landscape, PTFE’s non-stick properties and exceptional durability have made it indispensable across sectors ranging from aerospace to medical devices. Whether as a coating, fabric, or solid material, PTFE’s remarkable combination of properties – including chemical inertness, electrical insulation, and weather resistance – continues to drive innovation in sustainable manufacturing and advanced engineering solutions.
The material’s impact on European industry has been particularly significant, supporting the region’s leadership in sustainable technology development and precision manufacturing.
What is PTFE? Understanding the Basics
Chemical Structure and Composition
Polytetrafluoroethylene (PTFE) is a synthetic fluoropolymer consisting of carbon and fluorine atoms arranged in a unique molecular structure. The backbone of PTFE is made up of carbon atoms linked together in a chain, with each carbon atom bonded to two fluorine atoms. This creates a molecular formula of (C2F4)n, where ‘n’ represents the number of repeating units in the polymer chain.
What makes PTFE’s structure particularly remarkable is its high level of fluorination. The fluorine atoms completely surround the carbon backbone, creating a protective shield that contributes to the material’s exceptional chemical stability and non-stick properties. The carbon-fluorine bonds are among the strongest in organic chemistry, requiring significant energy to break.
This distinctive molecular arrangement results in PTFE’s characteristic properties: extremely low surface energy, high thermal stability, and remarkable chemical inertness. The strong bonds between atoms and the material’s crystalline structure also contribute to its excellent durability and resistance to environmental factors.
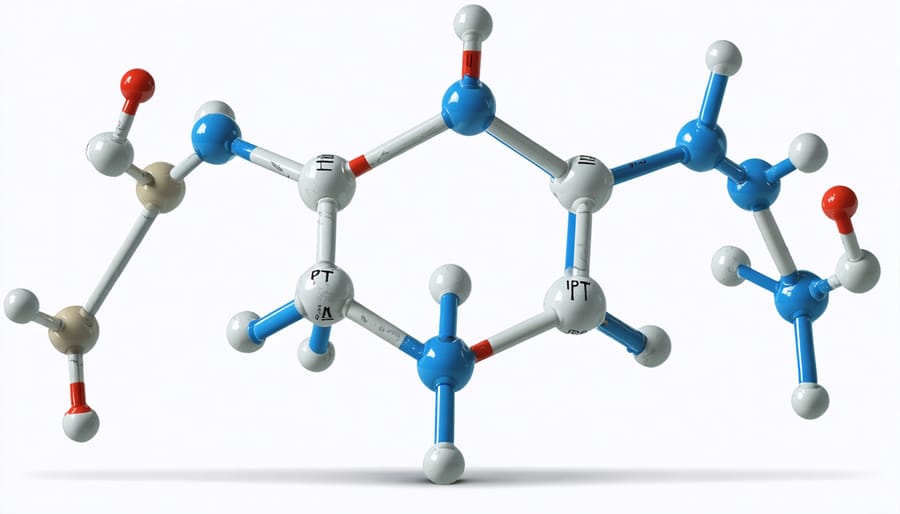
Key Physical Properties
PTFE exhibits remarkable physical properties that make it invaluable across various industries. Most notably, it maintains exceptional stability at temperatures ranging from -200°C to +260°C, making it ideal for extreme environments. Its non-stick characteristics arise from an incredibly low coefficient of friction, measured at 0.05-0.10, which is among the lowest of any solid material.
The material’s hydrophobic nature means it repels water effectively, while its chemical inertness ensures it remains stable when exposed to most acids, bases, and solvents. PTFE’s electrical insulating properties are exceptional, with a dielectric constant of 2.1, making it valuable for electrical applications.
With a density of approximately 2.2 g/cm³, PTFE offers a good balance of strength and weight. Its smooth, white appearance and ability to maintain these properties over long periods make it particularly suitable for long-term industrial applications. The material’s non-toxic nature and resistance to UV radiation further enhance its versatility.
PTFE in Fiberglass Fabric Applications
Manufacturing Process
The manufacturing of PTFE fiberglass fabric involves a sophisticated multi-step process that combines advanced polymer technology with precision engineering. Initially, high-grade fiberglass yarns are carefully woven into a base fabric using specialized industrial looms. This creates the robust foundation necessary for fiberglass fabric applications in demanding environments.
The crucial PTFE coating process follows, where the fabric undergoes multiple passes through a specialized coating line. During this phase, the material is impregnated with PTFE dispersion under carefully controlled temperature and tension conditions. The fabric then passes through high-temperature ovens, typically at 350-380°C, where the PTFE coating is sintered and permanently bonded to the fiberglass substrate.
Quality control measures are implemented throughout the process, including thickness measurements, surface uniformity checks, and mechanical property testing. The final product undergoes thorough inspection to ensure it meets rigorous European manufacturing standards and sustainability requirements, particularly for solar energy applications.
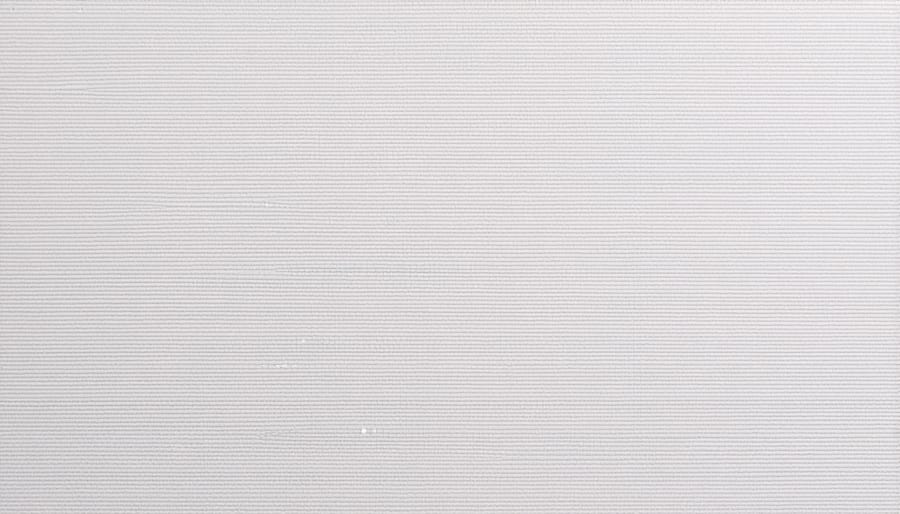
Performance Benefits
PTFE’s exceptional performance characteristics make it invaluable across various industrial applications, particularly in solar energy installations. In solar manufacturing environments, PTFE’s high temperature resistance enables smooth production processes, withstanding temperatures up to 260°C without degradation. This thermal stability ensures consistent performance even during intense heat exposure in solar panel assembly lines.
The material’s incredibly low friction coefficient (0.05-0.10) reduces wear and maintenance requirements in mechanical components, leading to longer equipment lifespans and reduced operational costs. In solar installations, PTFE-coated surfaces facilitate easier cleaning and maintenance, as dirt and debris struggle to adhere to its non-stick surface.
Furthermore, PTFE’s outstanding chemical resistance protects equipment from corrosive elements and harsh cleaning agents commonly used in industrial settings. Its electrical insulation properties make it ideal for protecting sensitive components in solar installations, while its UV resistance ensures longevity in outdoor applications.
When combined with fiberglass, PTFE creates composite materials that offer enhanced structural integrity while maintaining these beneficial properties, making it particularly valuable for long-term industrial installations across Europe’s diverse climate conditions.
Industrial Applications and Benefits
Solar Energy Applications
PTFE fiberglass fabric plays a crucial role in advancing solar energy installations across Europe, combining durability with exceptional performance characteristics. PTFE’s role in solar panel durability is particularly significant in both photovoltaic and concentrated solar power systems.
In photovoltaic applications, PTFE-coated fiberglass membranes serve as protective barriers, shielding solar panels from harsh environmental conditions while maintaining optimal light transmission. The material’s self-cleaning properties, derived from its non-stick nature, prevent dust and debris accumulation, ensuring consistent energy production efficiency.
For concentrated solar power installations, PTFE fiberglass fabric functions as a reflective surface material, directing sunlight towards collection points with minimal energy loss. Its thermal stability at extreme temperatures makes it ideal for solar tracking systems and thermal collection units, where maintaining structural integrity is paramount.
The material’s UV resistance and weatherability contribute to extended system lifespans, typically exceeding 25 years. This longevity, combined with minimal maintenance requirements, makes PTFE fiberglass fabric a cost-effective solution for solar energy projects. Its lightweight nature also reduces structural load requirements, simplifying installation processes and reducing overall project costs.
Innovation in PTFE technology continues to enhance solar energy efficiency, supporting Europe’s transition towards sustainable energy solutions while meeting stringent industry standards for performance and reliability.
Sustainability and Longevity
PTFE’s exceptional durability and sustainability credentials make it a standout choice for long-term applications, particularly in solar energy installations and industrial settings. With a lifespan that can exceed 20 years under normal conditions, PTFE significantly reduces the need for frequent replacements, minimizing waste and resource consumption.
The material’s chemical inertness means it doesn’t degrade or leach harmful substances into the environment, making it environmentally responsible for long-term installations. Its non-stick properties prevent the accumulation of dirt and contaminants, reducing the need for chemical cleaning agents and conserving water during maintenance.
Furthermore, PTFE’s energy-efficient properties contribute to sustainability goals. Its excellent thermal resistance and low friction characteristics help reduce energy consumption in mechanical applications. When used in architectural membranes and industrial components, PTFE’s reflective properties can enhance thermal efficiency, leading to reduced heating and cooling costs.
At the end of its service life, PTFE can be recycled through specialized processes, though this requires dedicated facilities. The material’s durability often means that components remain functional far beyond their intended lifespan, providing excellent value and reducing the environmental impact of replacement cycles.
PTFE stands as one of the most versatile and innovative materials in modern industry, combining exceptional chemical resistance with remarkable thermal stability. Its unique properties have revolutionized numerous applications, from industrial manufacturing to everyday consumer products. As sustainability becomes increasingly important, PTFE’s durability and long service life make it an environmentally conscious choice for many applications. Looking ahead, ongoing research continues to unlock new potential uses for PTFE, particularly in emerging technologies and green energy solutions. The material’s future appears promising, with developments in coating technologies and composite materials opening doors to even more efficient and sustainable applications. For industries and consumers alike, PTFE remains an indispensable material that continues to shape our technological landscape while meeting the growing demands for reliability and environmental responsibility.
Leave a Reply