Essential Solar Panel Materials That Make Your System Work
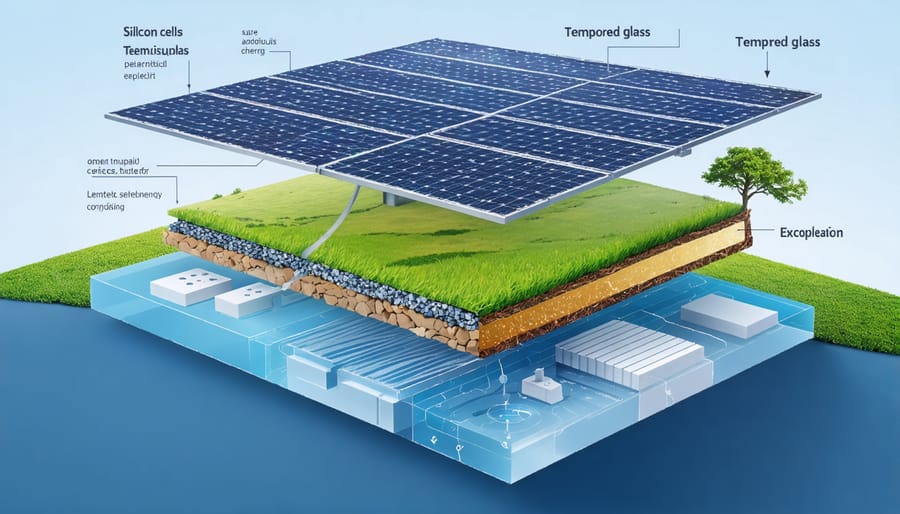
Solar panels represent a sophisticated fusion of precisely engineered materials working in harmony to convert sunlight into clean, renewable energy. From the photovoltaic cells at their core to the protective glass covering, each component plays a vital role in maximising energy production and ensuring long-term durability. Understanding these materials isn’t just about technical specifications—it’s about making informed decisions for sustainable energy solutions that meet European quality standards and performance requirements. Whether you’re planning a residential installation or industrial solar project, knowing the exact composition of solar panels helps ensure optimal performance, longevity, and return on investment. This comprehensive guide explores the essential materials that make up modern solar panels, from traditional silicon-based components to emerging technologies shaping the future of solar energy.
Core Materials in Modern Solar Panels
Silicon – The Heart of Solar Cells
Silicon stands as the fundamental building block of modern solar cells, with two primary variants dominating the market: monocrystalline and polycrystalline silicon. Monocrystalline silicon cells are crafted from a single crystal structure, offering superior efficiency rates of 15-22% and a distinctive dark, uniform appearance. These cells excel in space-constrained installations and perform remarkably well in European climate conditions.
Polycrystalline silicon cells, formed from multiple silicon fragments melted together, provide a cost-effective alternative with efficiency ratings of 13-17%. Their characteristic blue, multifaceted appearance results from the varied crystal formations within the material. While slightly less efficient, polycrystalline panels have gained significant market share across Europe due to their balanced performance-to-cost ratio.
Both silicon types undergo rigorous purification processes to achieve semiconductor-grade quality, essential for photovoltaic conversion. The choice between these variants often depends on specific installation requirements, available space, and budget considerations. European manufacturers have significantly advanced silicon processing techniques, achieving higher purity levels while reducing production costs and environmental impact.
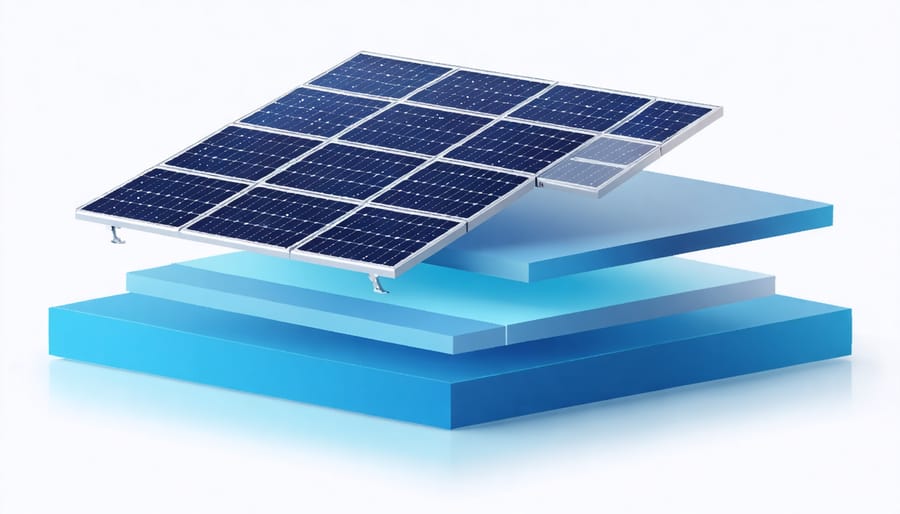
Glass and Encapsulation Materials
The outermost layer of solar panels consists of high-quality tempered glass and specialized encapsulation materials that serve as the first line of defense against environmental elements. These protective materials are crucial for ensuring the longevity and performance of solar installations across Europe’s diverse climate conditions.
The glass layer, typically 3.2mm to 4mm thick, is engineered to be highly transparent while offering excellent mechanical strength and impact resistance. It features anti-reflective coating technology that maximizes light transmission while protecting the underlying photovoltaic cells. Modern solar glass can transmit up to 94% of incoming light, significantly improving panel efficiency.
The encapsulation layer, commonly made from EVA (Ethylene Vinyl Acetate) or advanced polymer alternatives, seals the solar cells from moisture and provides crucial electrical insulation. This material bonds the glass, solar cells, and backsheet together, creating a weather-tight assembly that can withstand decades of exposure to sun, rain, and temperature variations. Recent innovations in encapsulation technology have enhanced UV stability and thermal management, contributing to longer panel lifespans and improved performance reliability.
Supporting Materials and Components
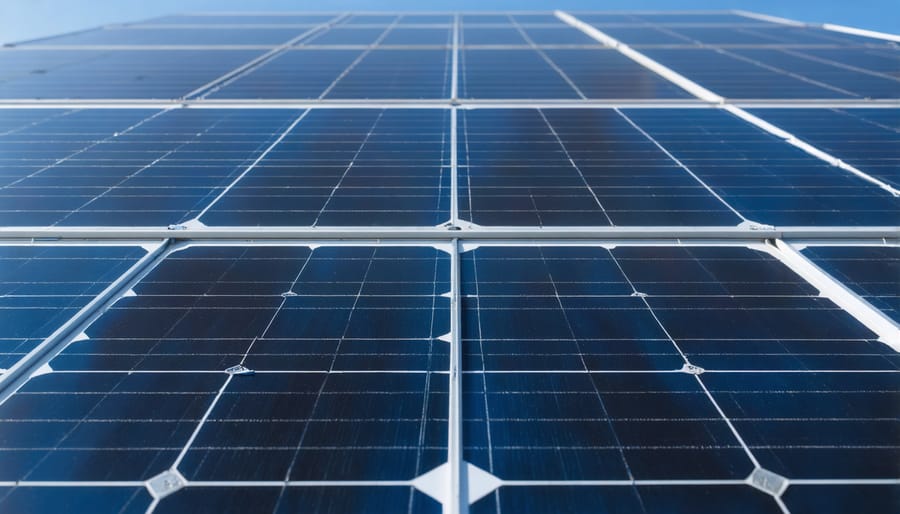
Metal Frame and Mounting Materials
The structural integrity of solar panels relies heavily on their metal frames and mounting systems, with aluminum being the primary material of choice across Europe. These frames provide essential protection for the solar cells and glass components while ensuring the entire assembly remains weatherproof and durable for decades of operation.
High-grade anodized aluminum frames form the panel’s exterior structure, offering excellent corrosion resistance and structural strength without adding excessive weight. These frames typically feature hollow chamber designs that optimize material usage while maintaining robust support capabilities.
The mounting hardware package usually includes:
– Aluminum rails for roof or ground mounting
– Stainless steel bolts, nuts, and washers
– Aluminum clamps (mid and end clamps)
– Roof attachment brackets
– Grounding components
– Cable management clips
European manufacturers often utilize marine-grade stainless steel (A2 or A4 grade) for fasteners to ensure maximum durability in coastal environments. The mounting systems are designed to withstand region-specific challenges, including heavy snow loads in Alpine regions and strong winds along coastal areas.
For optimal performance, manufacturers recommend using compatible mounting materials from the same supplier to ensure proper fit and maintain warranty coverage. The mounting system should comply with Eurocode standards and local building regulations, particularly concerning wind and snow load requirements specific to different European regions.
Wiring and Connection Materials
Proper wiring and connection materials are crucial for ensuring safe and efficient operation of your solar panel system. The primary components include solar cables, which are specially designed to withstand UV radiation and extreme weather conditions. These cables typically come in 4mm² or 6mm² sizes, with double insulation and high temperature resistance up to 120°C.
MC4 connectors are industry-standard components used to create secure, weatherproof connections between solar panels and other system elements. These connectors are designed for quick installation while maintaining excellent electrical contact and environmental protection.
Junction boxes, typically mounted on the back of solar panels, house the bypass diodes and provide connection points for the main cables. These boxes must be waterproof and UV-resistant to ensure long-term reliability.
For grounding purposes, you’ll need copper wire and grounding lugs that comply with European electrical standards. Cable ties, conduits, and cable clips are essential for proper cable management and protection against environmental factors.
Battery cables are required for systems with energy storage, typically using thicker gauges (25-95mm²) to handle higher currents. Terminal connectors, crimping tools, and appropriate fuses complete the electrical connection requirements.
Remember to select materials that meet IP65 or higher protection ratings for outdoor installations, and always ensure compliance with local electrical codes and EU standards for solar installations.
Advanced Materials for Enhanced Performance
Anti-Reflective Coatings
Anti-reflective coatings play a crucial role in maximising solar panel efficiency by reducing light reflection from the panel surface. These specialized coatings typically consist of silicon dioxide (SiO₂) or titanium dioxide (TiO₂), applied in ultra-thin layers to the glass surface of solar panels. When light hits an uncoated solar panel, up to 30% of it can be lost through reflection, but high-quality anti-reflective coatings can reduce this loss to less than 3%.
European manufacturers commonly use a multi-layer coating system, where each layer is precisely engineered to handle different wavelengths of light. The most advanced coatings incorporate nano-structured materials that mimic the surface of a moth’s eye, known for its superior anti-reflective properties. These innovative solutions not only improve energy absorption but also provide additional benefits like self-cleaning properties and enhanced durability.
The coating process typically involves vacuum deposition or sol-gel techniques, ensuring uniform coverage and optimal thickness for maximum light transmission. Modern anti-reflective coatings can last the entire 25-30 year lifespan of quality solar panels, contributing significantly to sustained energy production efficiency.
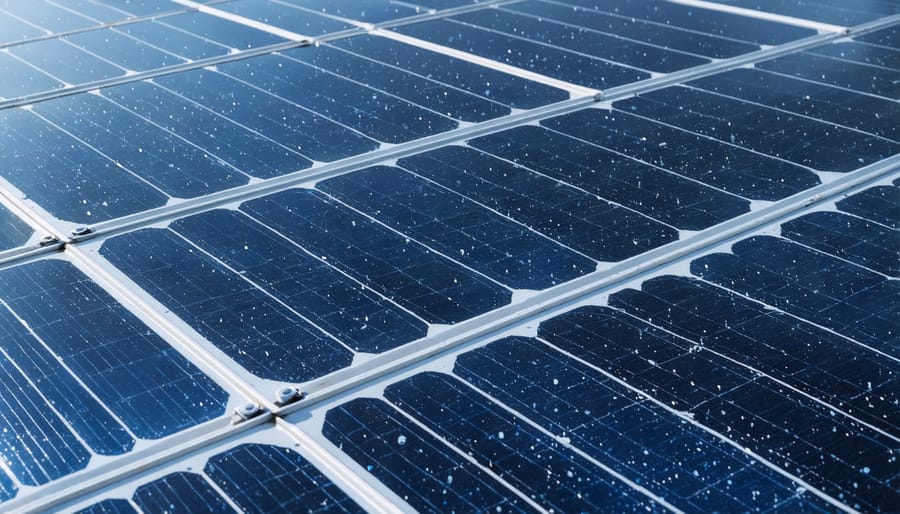
Back Sheet Technologies
The back sheet serves as the final protective layer of a solar panel, playing a crucial role in its durability and performance. Traditionally, most manufacturers use multi-layer polymer composites, with TPT (Tedlar-PET-Tedlar) being the industry standard. This three-layer structure combines weather resistance with excellent electrical insulation properties.
Recent innovations have introduced fluorine-free back sheets, addressing environmental concerns while maintaining protective qualities. These sustainable alternatives, including KYNAR® PVDF-based materials and advanced polyolefin composites, are gaining popularity across European installations.
The back sheet must withstand harsh weather conditions, UV radiation, and temperature fluctuations while preventing moisture ingress. Modern variants incorporate reflective properties to enhance light capture and improve overall panel efficiency. Some manufacturers now offer coloured back sheets, allowing better architectural integration without compromising protection.
When selecting back sheet materials, European installers should prioritise products certified to IEC standards, ensuring long-term reliability and optimal performance throughout the panel’s lifecycle.
Material Quality and European Standards
In the European solar industry, adherence to stringent material quality standards is paramount for ensuring the longevity and performance of solar installations. All materials used in solar panel manufacturing must comply with IEC 61215 and IEC 61730 certifications, which verify durability and safety requirements. These standards encompass everything from silicon purity levels to the quality of EVA encapsulation materials.
Key European certification bodies, including TÜV Rheinland and SGS, regularly assess manufacturing processes and material quality. Solar glass must meet EN 12150 standards for mechanical strength and thermal resistance, while frame materials require compliance with EN AW-6063 T5 specifications for aluminum grade and treatment.
The RoHS (Restriction of Hazardous Substances) directive further ensures that materials used are environmentally sustainable and safe for long-term deployment. Quality control extends to junction boxes and connecting materials, which must meet IP65 or IP67 ratings for weather resistance.
For optimal performance and reliability, manufacturers must provide detailed material documentation, including certificates of analysis and performance test results. This comprehensive quality assurance system helps maintain the high standards expected in the European solar market while supporting the continent’s renewable energy objectives.
The careful selection of solar panel materials plays a pivotal role in determining the efficiency, durability, and sustainability of solar energy systems. As European markets continue to embrace renewable energy solutions, the evolution of material science offers promising developments for the future of solar technology. Advanced manufacturing techniques and innovative materials are driving improvements in panel efficiency while reducing production costs and environmental impact.
Looking ahead, emerging trends point towards more sustainable material choices, including lead-free alternatives and recycled components, aligning with European Union’s circular economy initiatives. The integration of bifacial technology and enhanced anti-reflective coatings suggests a future where solar panels will become increasingly efficient and adaptable to diverse installation environments.
For property owners and businesses considering solar installation projects, understanding material options ensures informed decision-making and optimal system performance. As the industry continues to innovate, we can expect to see new materials and composites that further improve durability, increase energy conversion rates, and reduce the overall carbon footprint of solar panel production. This ongoing evolution in material science reinforces solar energy’s position as a cornerstone of Europe’s sustainable energy future.
Leave a Reply