Industrial Solar Heat: Transform Your Manufacturing with Solar Thermal Power
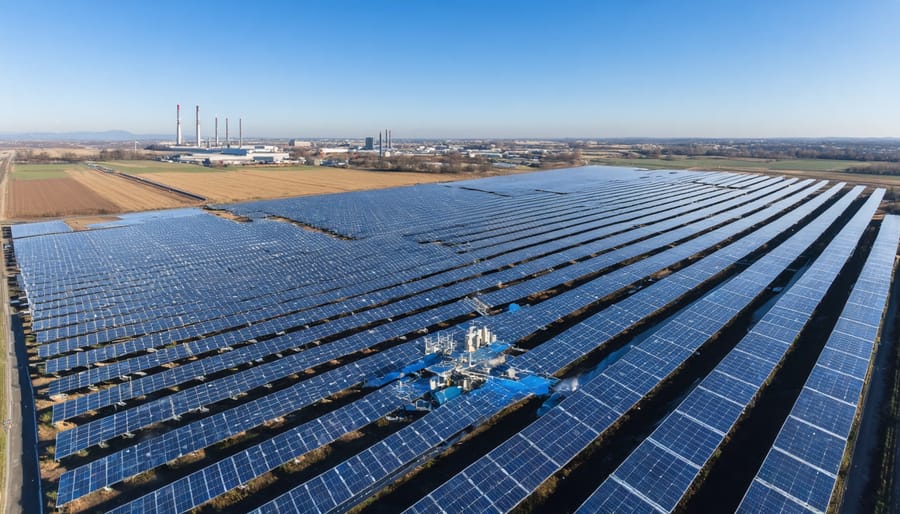
Industrial solar systems are revolutionizing manufacturing and processing facilities across Europe, delivering unprecedented energy autonomy while slashing operational costs. As solar solutions for European industries continue to advance, these installations now power everything from pharmaceutical production to food processing at temperatures reaching 400°C. The technology’s maturity, combined with declining installation costs and generous EU incentives, has created a perfect storm for industrial adoption.
Modern industrial solar arrays integrate seamlessly with existing heat networks, utilizing advanced thermal storage systems to maintain consistent energy supply during non-sunlight hours. This reliability, coupled with typical payback periods of 3-7 years, makes industrial solar systems an increasingly attractive investment for forward-thinking facility managers. From Sweden’s solar-powered district heating networks to Spain’s solar thermal industrial parks, these systems are proving their worth in diverse applications across the continent.
By replacing or supplementing conventional fossil fuel systems, industrial solar installations not only reduce carbon footprints but also provide a hedge against volatile energy prices, offering both environmental and financial sustainability for decades to come.
Understanding Industrial Solar Thermal Systems
Core Components
Industrial solar systems rely on three essential components that work in harmony to deliver reliable thermal energy. Solar collectors, available in various designs including flat-plate and evacuated tube variants, serve as the primary energy capture devices. These collectors are engineered to maximize solar radiation absorption while minimizing heat loss, achieving operating temperatures up to 400°C for industrial processes.
The heat transfer system forms the crucial link between collection and utilization. It consists of highly efficient pumps, heat exchangers, and specialized piping networks that transport thermal energy using carefully selected heat transfer fluids. These fluids, ranging from water-glycol mixtures to synthetic oils, are chosen based on specific temperature requirements and operating conditions.
Thermal storage solutions complete the system by ensuring consistent energy availability. Modern storage systems utilize advanced materials like phase change materials (PCMs) or molten salts to maintain process temperatures during non-sunny periods. These storage units can be configured as buffer tanks for daily operation or seasonal storage for long-term energy management, providing industries with reliable thermal energy around the clock.
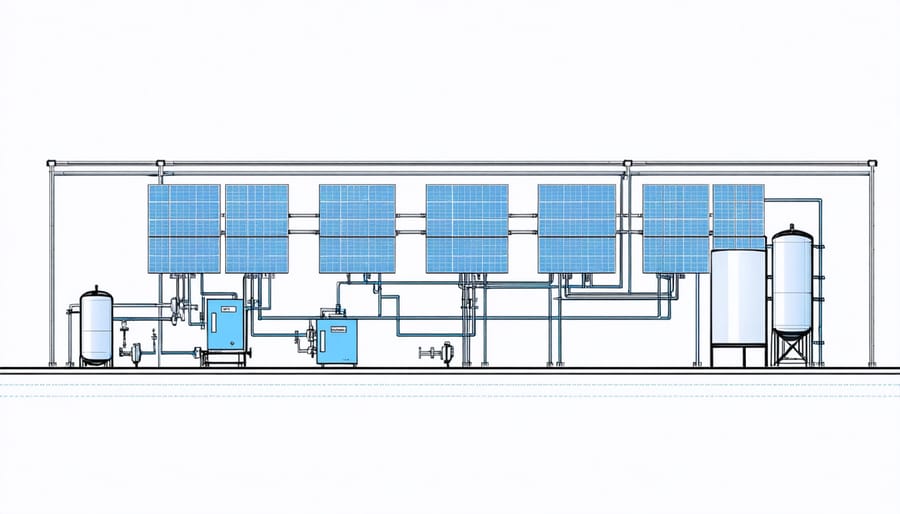
Integration Points
Industrial solar systems seamlessly integrate with existing manufacturing processes through carefully designed connection points and control systems. The primary integration occurs at the heat exchange interface, where solar-heated transfer fluids connect with industrial process lines. This integration can be achieved through direct or indirect heat exchange methods, depending on the specific requirements of the facility.
Modern industrial solar installations feature sophisticated monitoring and control systems that ensure optimal coordination between solar thermal components and conventional heating systems. These systems can automatically adjust flow rates, temperatures, and energy distribution based on real-time process demands and solar availability.
Key integration considerations include the modification of existing piping systems, installation of additional heat exchangers, and implementation of backup systems for continuous operation. The integration process typically requires minimal disruption to ongoing operations, as most connections can be made during planned maintenance periods.
For maximum efficiency, industrial solar systems can be integrated at multiple points within a facility, serving different processes simultaneously. This approach optimizes energy utilization and increases the overall return on investment while supporting sustainable manufacturing practices.
Key Industrial Applications
Process Heating
Process heating represents one of the most significant applications of industrial solar systems, transforming manufacturing processes across Europe. These systems can effectively generate temperatures up to 400°C, making them ideal for various industrial operations, from food processing to textile manufacturing.
The technology typically employs concentrated solar collectors that focus sunlight onto specialized thermal receivers, converting solar energy into usable heat. This heat can be directly integrated into existing industrial processes or stored in thermal storage systems for use during non-sunny periods.
Common applications include preheating boiler feed water, steam generation for sterilization, drying processes in the food industry, and heat treatment in metal processing. For instance, dairy facilities use solar thermal systems to maintain precise temperatures for pasteurization, while textile manufacturers employ them for dying and finishing processes.
The integration of solar process heating can reduce operational costs significantly while supporting sustainability goals. Modern systems feature advanced controls that ensure consistent heat delivery and seamless integration with conventional heating systems. This reliability, combined with the potential for substantial CO2 emissions reduction, makes solar process heating an increasingly attractive option for forward-thinking industrial operations.
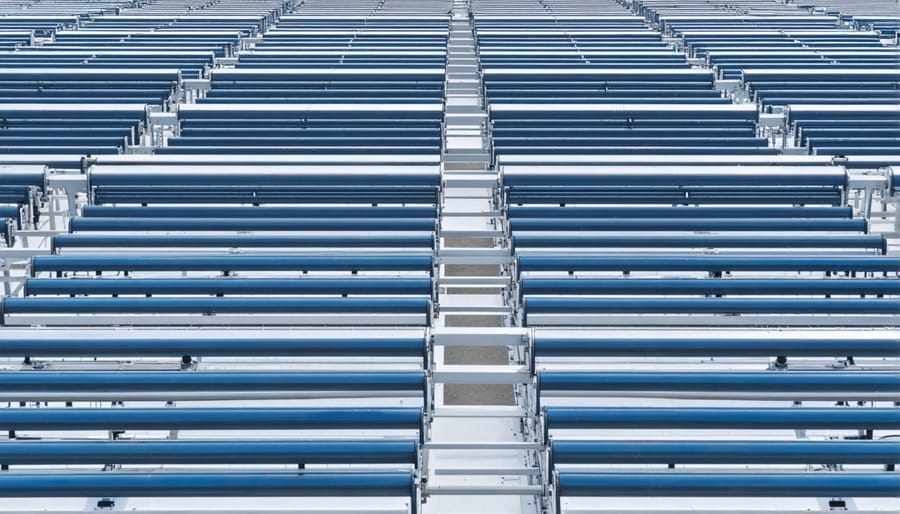
Steam Generation
Industrial solar thermal systems harness the sun’s energy to generate high-temperature steam, a vital component in numerous manufacturing processes. The process begins with specially designed solar collectors, typically parabolic troughs or Fresnel reflectors, which concentrate sunlight onto receiver tubes containing a heat transfer fluid. This fluid, often synthetic oil or molten salt, is heated to temperatures ranging from 150°C to 400°C.
The heated fluid then flows through a heat exchanger, where it transfers its thermal energy to water, converting it into steam. This solar-generated steam can achieve industrial-grade pressures and temperatures suitable for various applications, from food processing to chemical manufacturing.
Modern steam generation systems incorporate advanced controls and storage solutions to maintain consistent output, even during periods of variable solar radiation. Thermal storage tanks filled with molten salt can extend operation beyond daylight hours, providing industries with reliable steam supply.
The efficiency of these systems has improved significantly, with some installations achieving solar-to-steam conversion rates of up to 75%. This high efficiency, combined with reduced operational costs and carbon emissions, makes solar steam generation an attractive option for industries across Europe. Many facilities integrate these systems with existing conventional boilers, creating hybrid setups that ensure continuous steam availability while maximizing renewable energy usage.
Economic Benefits and ROI
Energy Cost Reduction
Industrial solar systems offer substantial cost-saving potential through reduced energy expenses. A typical industrial installation can decrease energy costs by 30-60%, depending on the facility’s location, energy consumption patterns, and system size. The initial investment is often offset within 4-7 years through these savings, making it an attractive long-term investment.
To calculate potential savings, businesses should consider their current energy consumption, peak usage periods, and local solar irradiance levels. For instance, a manufacturing facility consuming 500,000 kWh annually might save €45,000-€75,000 per year on energy costs with a properly sized solar system.
European businesses can also benefit from various regional incentives and feed-in tariffs, further improving the financial outlook. Many countries offer tax benefits, grants, and accelerated depreciation schemes for industrial solar installations. When combined with rising conventional energy costs and improved solar technology efficiency, the economic advantages become even more compelling.
Modern monitoring systems allow precise tracking of energy production and savings, helping businesses optimize their return on investment and validate their sustainability initiatives.
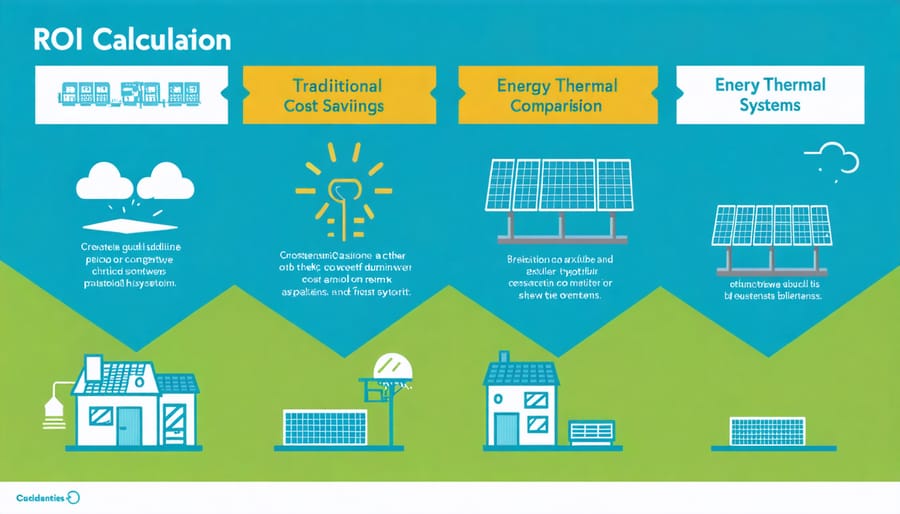
Available Incentives
The European Union and individual member states offer substantial renewable energy incentives to support industrial solar thermal adoption. Key programs include the Innovation Fund, which provides grants covering up to 60% of additional capital costs for large-scale installations, and the European Regional Development Fund (ERDF), offering targeted support for regional industrial development projects.
Many countries complement these EU-wide initiatives with national schemes. Germany’s Market Incentive Programme (MAP) provides attractive funding rates for industrial solar thermal systems, while France’s Fonds Chaleur offers comprehensive support for heat production from renewable sources. Spain’s thermal innovation programs focus particularly on industrial process heat applications.
Additionally, the European Investment Bank (EIB) provides preferential loans and technical assistance through the European Local Energy Assistance (ELENA) facility, helping industries develop bankable solar thermal projects. These financial instruments, combined with carbon pricing mechanisms and energy efficiency obligations, create a robust framework supporting the transition to sustainable industrial heating solutions.
Implementation Success Stories
Manufacturing Case Study
In 2021, Schneider Electric’s manufacturing facility in Grenoble, France, embarked on an ambitious solar project that showcases the potential of industrial solar systems. The 12,000-square-meter facility, which produces electrical components, installed a 1.3 MW rooftop solar array combined with smart energy management systems.
The installation consists of 3,200 high-efficiency solar panels, strategically positioned to maximize exposure to sunlight while working around existing HVAC systems and skylights. The system was designed to meet 40% of the facility’s annual electricity needs, with peak production occurring during summer months when cooling demands are highest.
What makes this case particularly noteworthy is the integration of smart monitoring technology. Real-time data analysis allows facility managers to optimize energy consumption patterns, matching production schedules with peak solar generation periods. The system has exceeded initial expectations, reducing the facility’s carbon emissions by 850 tonnes annually and cutting energy costs by 32%.
The project’s success prompted Schneider Electric to implement similar systems across their European manufacturing network. The installation paid for itself in just 6.5 years, thanks to combined energy savings and government incentives. This case demonstrates how industrial solar systems can deliver both environmental and economic benefits while maintaining reliable power supply for critical manufacturing operations.
Food Processing Example
A leading food processing facility in Bavaria, Germany, showcases the remarkable potential of industrial solar thermal systems. In 2019, the facility, which specializes in dairy products, implemented a large-scale solar thermal installation to reduce its dependence on conventional heating methods for its pasteurization processes.
The system consists of 128 high-efficiency solar thermal collectors, covering approximately 460 square meters of roof space. These collectors generate hot water at temperatures between 60°C and 85°C, which is ideal for various food processing applications, including cleaning, sterilization, and pasteurization.
Since its implementation, the facility has achieved a 42% reduction in natural gas consumption for heating processes. This translates to annual energy savings of approximately 280,000 kWh and a reduction of 65 tonnes in CO2 emissions. The financial impact has been equally impressive, with operational costs decreasing by €32,000 annually.
The project’s success stems from careful system integration with existing processes and sophisticated control systems that optimize solar energy utilization. The installation included thermal storage tanks that maintain consistent temperatures during cloudy periods, ensuring uninterrupted production.
The facility’s experience demonstrates that solar thermal technology can effectively meet industrial process heat requirements while significantly reducing operational costs and environmental impact. The project’s five-year payback period, supported by regional renewable energy incentives, makes it a compelling case study for other food processing operations considering sustainable energy solutions.
Future-Proofing Your Industry
As industries across Europe face increasing pressure to reduce their carbon footprint, implementing solar thermal systems has become a strategic necessity rather than just an environmental choice. Recent industrial solar innovations are paving the way for businesses to meet both current and future sustainability requirements.
The European Union’s commitment to achieving climate neutrality by 2050 means stricter energy regulations are inevitable. Industrial solar thermal systems position companies ahead of these upcoming changes, ensuring compliance while maintaining operational efficiency. By investing in solar technology today, businesses can avoid costly retrofits and regulatory penalties tomorrow.
These systems also align perfectly with the growing demand for sustainable manufacturing processes. Consumers and business partners increasingly prioritize environmental responsibility, making solar thermal installations a valuable asset for maintaining market competitiveness. Companies that embrace solar solutions often find themselves better positioned to secure contracts and partnerships, particularly with organizations that have strict sustainability requirements.
Moreover, industrial solar thermal systems offer scalability and adaptability. As technology advances, these installations can be upgraded and expanded to meet growing energy demands or integrate with newer renewable energy solutions. This flexibility ensures that initial investments continue to deliver value even as energy needs evolve.
The integration of smart monitoring systems and predictive maintenance capabilities further enhances the future-ready aspect of solar thermal installations. These features allow facilities to optimize performance, reduce operational costs, and extend system lifespan, making them an increasingly attractive solution for forward-thinking industries.
Industrial solar thermal systems represent a significant opportunity for European businesses to enhance their sustainability profile while achieving substantial cost savings. The combination of reduced energy expenses, decreased carbon emissions, and improved operational efficiency makes these systems an attractive investment for forward-thinking industries. With current EU incentives and support programs, the financial barriers to implementation have never been lower.
For industries considering solar thermal solutions, the path forward begins with a comprehensive site assessment and energy audit. This enables precise system sizing and optimal integration with existing processes. Working with experienced solar thermal specialists ensures smooth project implementation and maximizes return on investment.
As Europe continues its transition towards renewable energy, industrial solar systems stand out as a proven technology that delivers immediate benefits while supporting long-term sustainability goals. The scalability and adaptability of these systems, combined with ongoing technological innovations, provide industries with a future-proof solution for their thermal energy needs.
To take the first step towards implementing an industrial solar thermal system, connect with qualified providers who can assess your facility’s specific requirements and develop a tailored solution that meets your operational and financial objectives.
Leave a Reply