How Solar Panel Manufacturing is Slashing Its Carbon Footprint (And Why It Matters)
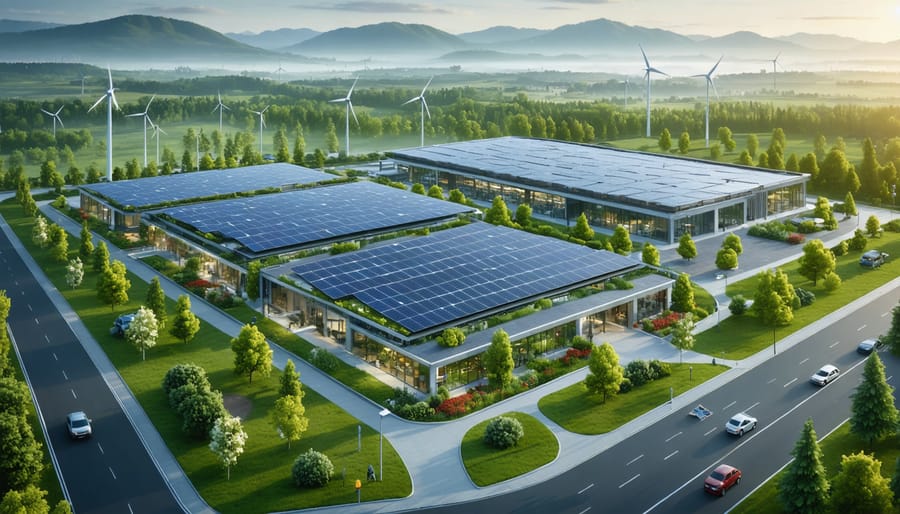
Solar panels revolutionize clean energy production, yet their manufacturing process raises important questions about environmental impact. As Europe leads the charge in sustainable manufacturing, the carbon footprint of solar panel production has decreased by 80% over the past decade through breakthrough innovations in materials and processes.
A typical solar panel installation now offsets its manufacturing emissions within 1-2 years of operation, generating clean electricity for 25+ years afterward. This remarkable payback period represents a significant advancement from earlier generations of solar technology, where environmental break-even could take 4-5 years.
European manufacturers are pioneering low-carbon production methods, from recycled silicon usage to renewable-powered facilities. These innovations address the full lifecycle impact of solar technology while maintaining the high performance standards that European solar installations are known for. With carbon-conscious manufacturing becoming increasingly important to consumers and businesses alike, understanding the environmental impact of solar panels has never been more crucial for making informed energy decisions.
The drive toward carbon-neutral solar manufacturing aligns perfectly with the EU’s ambitious climate goals, positioning European solar technology at the forefront of truly sustainable energy solutions.
The Carbon Reality of Solar Panel Production
Current Manufacturing Emissions
The carbon cost of solar manufacturing remains a significant consideration in the industry’s environmental impact assessment. Current production processes typically generate between 40-50g of CO2 emissions per kilowatt-hour of energy produced, primarily from energy-intensive silicon purification and panel assembly. The majority of these emissions stem from fossil fuel-powered manufacturing facilities, particularly in regions where coal remains a primary energy source.
European manufacturing facilities average lower emissions, at approximately 35g CO2/kWh, due to cleaner energy grids and stringent environmental regulations. The most substantial environmental impact occurs during silicon processing, which requires temperatures exceeding 1,400°C. Additional emissions sources include aluminum frame production, glass manufacturing, and transportation logistics.
Despite these current challenges, it’s important to note that solar panels typically offset their manufacturing emissions within 1-2 years of operation in European conditions, representing a significant improvement from previous decades. Modern manufacturing innovations and increased energy efficiency continue to drive these numbers lower, particularly in European facilities implementing sustainable production practices.
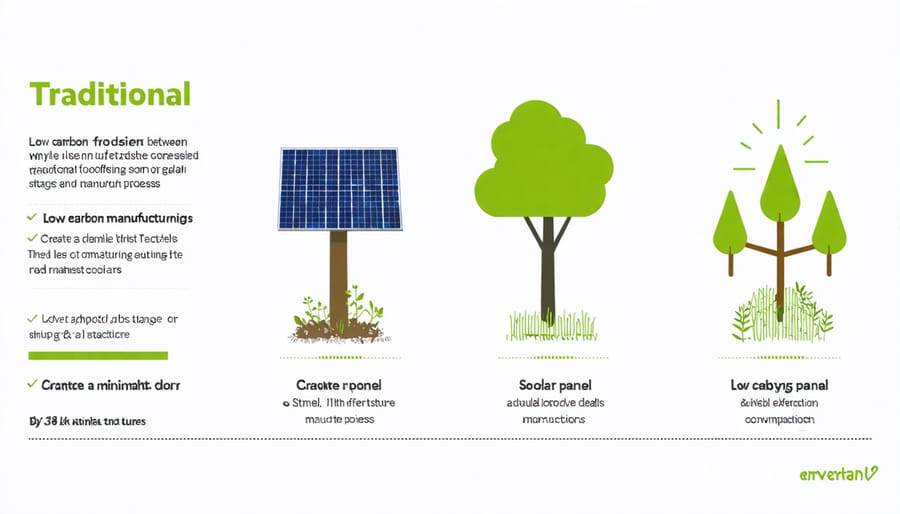
Energy Payback Time
Solar panels typically achieve their energy payback period within 1-3 years, depending on the installation location and panel technology. This means that the energy used to manufacture, transport, and install the panels is offset by the clean energy they produce within this timeframe. In Southern European regions, where solar irradiance is higher, panels can reach this milestone even faster, sometimes in less than a year.
Modern manufacturing innovations have significantly reduced the energy intensity of solar panel production. Today’s efficient production methods mean that a typical residential solar installation will generate 20-30 times more energy during its lifetime than was required for its manufacturing. This positive energy balance makes solar panels one of the most environmentally sound energy investments available.
For perspective, considering that most solar panels have a lifespan of 25-30 years, they spend over 90% of their operational life generating completely clean energy after paying back their initial carbon debt. This remarkable ratio continues to improve as manufacturing processes become increasingly energy-efficient and sustainable.
Innovative Manufacturing Solutions
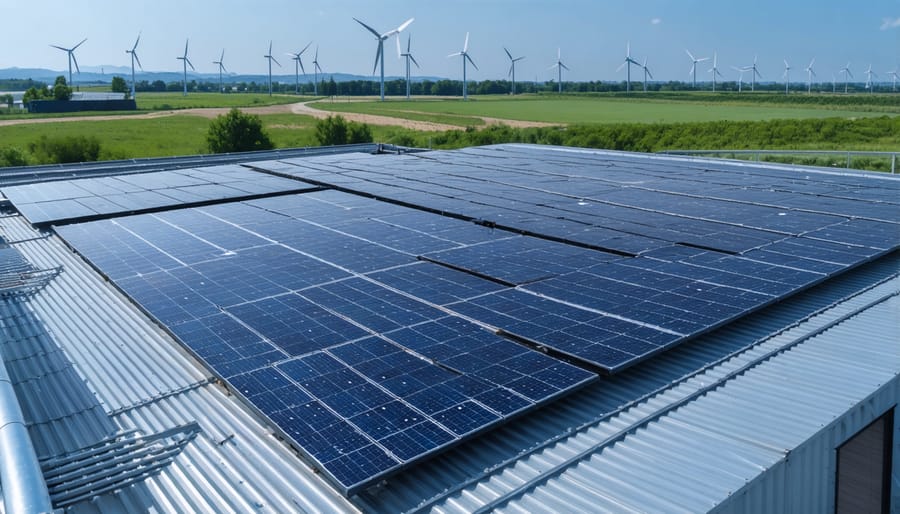
Renewable Energy in Production
Leading solar panel manufacturers are increasingly powering their production facilities with renewable energy sources, significantly reducing the carbon footprint of solar panel manufacturing. This shift towards clean energy in production represents a crucial step in making solar technology truly sustainable from cradle to grave.
Several major European manufacturers now operate facilities that run predominantly on solar and wind power. For instance, facilities in Germany and Spain have installed large-scale rooftop solar arrays that provide up to 40% of their daily operational energy needs. Some manufacturers have gone further by establishing direct partnerships with wind farms and hydroelectric plants to ensure a consistent supply of renewable energy.
This transition to clean energy in manufacturing has yielded impressive results. Recent industry data shows that factories powered by renewable energy can reduce the carbon footprint of solar panel production by up to 50% compared to conventional manufacturing methods. Advanced energy management systems and smart grid integration enable these facilities to optimise their energy consumption patterns, maximising the use of available renewable resources.
Moreover, manufacturers are implementing innovative energy storage solutions to address intermittency issues, ensuring continuous production even during periods of low renewable energy generation. This comprehensive approach to sustainable manufacturing not only reduces environmental impact but also helps decrease the energy payback time of solar panels, making them an even more attractive solution for climate-conscious consumers.
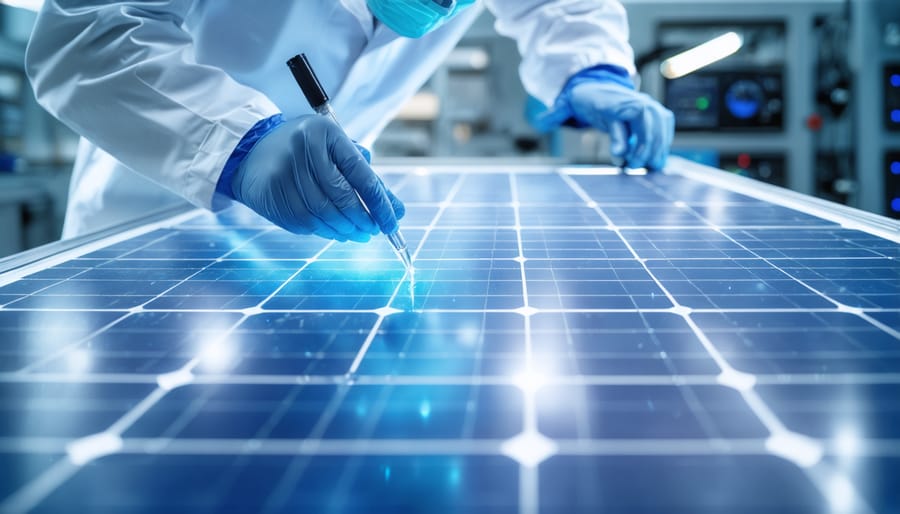
Material Innovation
Recent breakthroughs in material science are revolutionising how we manufacture solar panels, significantly reducing their carbon footprint. Innovative silicon alternatives, such as perovskite-based cells, require less energy-intensive production processes while maintaining high efficiency levels. These advancements are particularly prominent in European research facilities, where scientists have developed thin-film technologies that use just 1% of the silicon needed in traditional panels.
The industry is also making significant strides in sustainable material recycling, with new techniques enabling the recovery of up to 95% of valuable materials from end-of-life panels. Advanced manufacturing processes now incorporate recycled silicon and glass, creating a circular economy approach that substantially reduces raw material demands.
Particularly promising are bio-based encapsulation materials that replace traditional petroleum-derived components. These plant-based alternatives not only reduce dependency on fossil fuels but also improve panel degradability at end-of-life. European manufacturers are leading this transition, implementing water-based coating processes that eliminate harmful solvents and reduce production emissions by up to 50%.
These material innovations, combined with automated manufacturing processes and localised production facilities, are helping to create a new generation of solar panels with significantly lower embodied carbon content, while maintaining the high performance standards that European consumers expect.
European Leadership in Green Manufacturing
Europe has emerged as a global leader in sustainable solar panel manufacturing, with numerous initiatives driving innovation in low-carbon production methods. Countries like Germany, France, and Norway are pioneering breakthrough technologies that significantly reduce the carbon footprint of solar panel manufacturing processes.
The European Solar Manufacturing Council has established stringent environmental guidelines, encouraging manufacturers to adopt renewable energy in their production facilities. Many European factories now operate on 100% renewable energy, creating a virtuous cycle where solar panels are manufactured using solar power.
Notable achievements include the development of kerf-less wafer cutting techniques that reduce silicon waste by up to 50%, and the implementation of closed-loop water recycling systems that minimize resource consumption. Advanced automation and energy-efficient manufacturing processes have further reduced the carbon intensity of production.
The EU’s Green Deal has catalyzed investment in research and development, leading to innovations in recycled materials usage and extended product lifecycles. European manufacturers are also leading the way in establishing transparent supply chains and comprehensive environmental impact assessments.
These initiatives have resulted in solar panels with significantly lower embodied carbon compared to global averages. European manufacturers typically achieve carbon payback periods of less than two years, setting new industry standards for sustainable production while maintaining high performance and reliability.
Measuring and Certifying Carbon Reduction
Carbon Footprint Metrics
The carbon footprint of solar panels is measured through comprehensive Life Cycle Assessment (LCA), which evaluates environmental impacts from raw material extraction through manufacturing, transport, installation, operation, and end-of-life disposal. Key metrics include energy payback time (EPBT), typically ranging from 1-4 years in European conditions, and carbon dioxide equivalent emissions (CO2e) per kilowatt-hour of electricity generated.
Manufacturing processes account for approximately 80% of a solar panel’s total carbon footprint. Primary contributors include silicon purification, which requires high temperatures and energy-intensive processes, and the production of aluminium frames and glass components. On average, manufacturing a standard residential solar panel generates between 300-500 kg of CO2e emissions.
European manufacturers are increasingly adopting standardised measurement protocols, such as Product Environmental Footprint (PEF) guidelines, to ensure accurate and comparable carbon footprint calculations. These assessments consider factors like transportation distances, manufacturing energy sources, and material recycling rates.
Modern solar panels typically generate 20-50g of CO2e per kilowatt-hour of electricity produced over their lifetime, compared to 300-1000g for fossil fuel alternatives. This measurement includes both direct emissions and indirect factors such as maintenance and eventual recycling requirements. The industry continues to improve these metrics through technological innovations and more efficient manufacturing processes.
European Certification Standards
European certification standards play a vital role in ensuring solar panels meet rigorous environmental and quality benchmarks throughout their lifecycle. The IEC 61730 and IEC 61215 standards form the foundation of solar panel certification in Europe, establishing crucial safety and performance requirements. These certifications evaluate factors including manufacturing processes, material sourcing, and end-of-life recyclability.
The Solar Keymark certification, specifically developed for the European market, provides comprehensive validation of a solar panel’s carbon footprint and environmental impact. This certification considers the entire production chain, from raw material extraction to manufacturing processes, ensuring compliance with EU sustainability guidelines.
Manufacturers must also adhere to the RoHS (Restriction of Hazardous Substances) directive, which limits the use of harmful materials in electronic equipment. The WEEE (Waste Electrical and Electronic Equipment) directive further ensures responsible end-of-life management and recycling of solar panels.
The ECO-design directive and Energy labelling framework have recently introduced specific requirements for solar panels, focusing on energy efficiency during production and transparency in environmental impact reporting. These standards not only guarantee product quality but also drive innovation in low-carbon manufacturing processes.
For consumers and businesses, these certifications provide assurance that their solar investment aligns with European environmental objectives while maintaining high performance standards. Regular audits and updates to these certifications ensure continuous improvement in the industry’s environmental practices.
Future Developments
The solar panel manufacturing industry is rapidly evolving, with innovative technologies promising to significantly reduce carbon footprints. European manufacturers are leading the charge towards zero carbon manufacturing goals through several groundbreaking developments.
Perovskite solar cells represent one of the most promising advancements, offering the potential for higher efficiency while requiring less energy-intensive production processes. These next-generation cells can be manufactured at lower temperatures, reducing energy consumption during production by up to 50% compared to traditional silicon cells.
Recycled silicon is gaining traction as a primary material source, with new purification techniques making it increasingly viable for high-performance panels. This circular approach could reduce manufacturing emissions by up to 30% while addressing the growing concern of solar panel waste.
Automated manufacturing powered by renewable energy is becoming more prevalent, with smart factories incorporating AI-driven quality control and energy management systems. These facilities are achieving unprecedented levels of efficiency while maintaining strict environmental standards.
Emerging thin-film technologies are showing promise in reducing material usage while maintaining high performance. Advanced coating techniques and material innovations are enabling manufacturers to create panels that require fewer raw materials and less energy during production.
Water-free cleaning processes and dry etching techniques are being developed to minimize resource consumption during manufacturing. These innovations could reduce water usage by up to 90% in panel production while improving overall efficiency.
Looking ahead, the integration of carbon capture technologies in manufacturing facilities and the development of biodegradable panel components are set to further reduce the industry’s environmental impact. European manufacturers are also investigating alternative packaging solutions and transportation methods to create a truly sustainable supply chain.
These developments are not just technological achievements but represent a fundamental shift towards sustainable manufacturing practices that will shape the future of solar energy production.
The drive to reduce the carbon footprint of solar panel manufacturing represents a crucial step towards truly sustainable renewable energy. As the solar industry continues to mature, manufacturers are making significant strides in implementing cleaner production processes, utilizing renewable energy in factories, and developing innovative recycling solutions. These improvements are steadily decreasing the carbon payback time of solar panels, making them an increasingly attractive option for environmentally conscious European businesses and homeowners.
The industry’s commitment to sustainable manufacturing practices not only benefits the environment but also strengthens the economic case for solar adoption. By reducing energy consumption in production and optimizing material usage, manufacturers are creating more efficient panels while simultaneously lowering their environmental impact. This dual benefit of improved performance and reduced carbon footprint is essential for achieving Europe’s ambitious climate goals.
Looking ahead, the continued focus on reducing carbon emissions in solar panel production will play a vital role in accelerating the transition to renewable energy. As manufacturing processes become cleaner and more efficient, solar panels will further cement their position as a cornerstone of sustainable energy solutions. The industry’s dedication to environmental responsibility ensures that solar power remains not just a renewable energy source, but a truly sustainable one that considers its entire lifecycle impact.
Leave a Reply